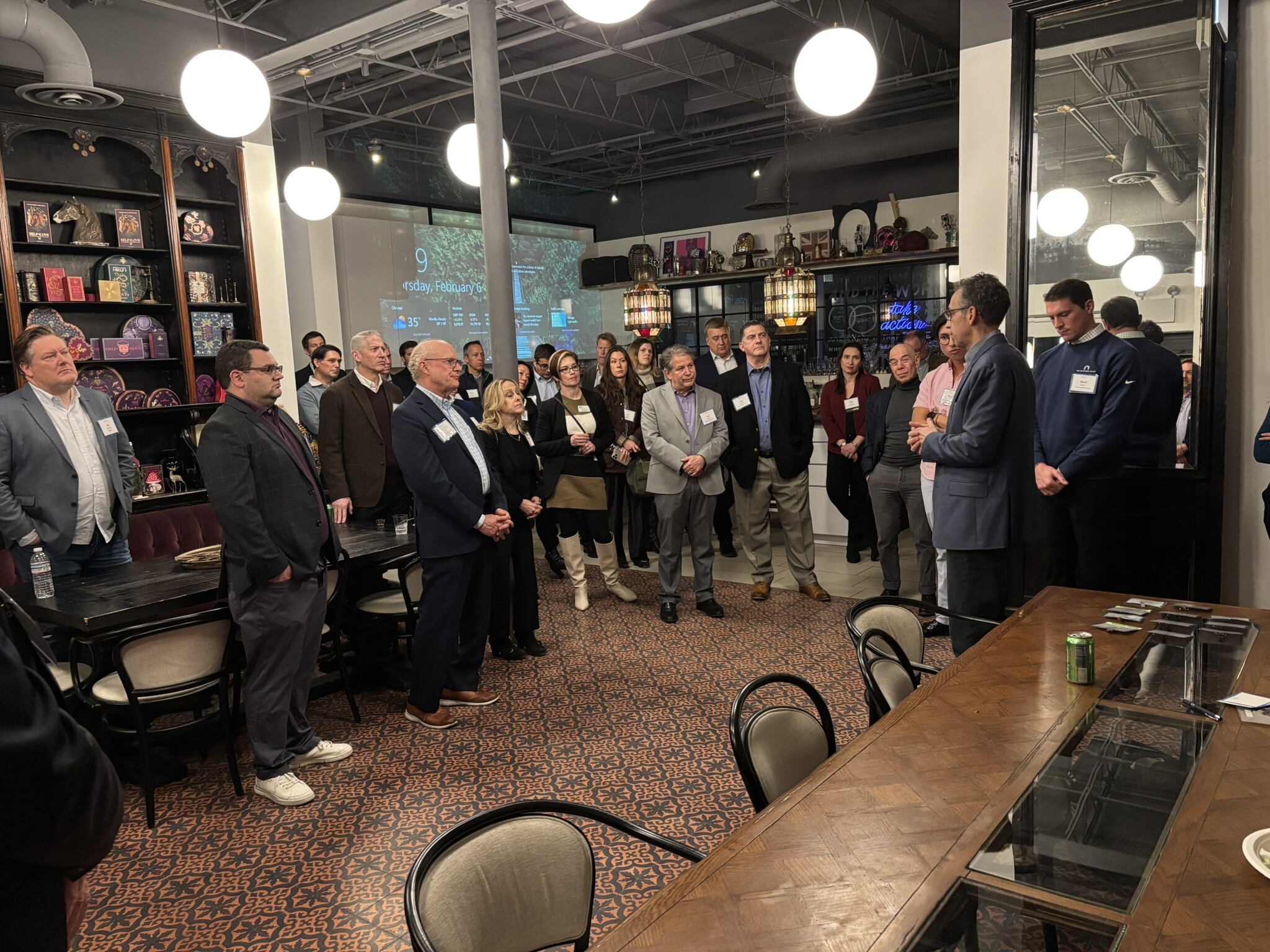
Take Action
I had the distinct honor of attending an ACG Chicago event at the Vosges Haut-Chocolat facility in Chicago, IL. Outside of the fabulous chocolate and drink pairing, we had the opportunity to hear the CEO, Andy Ruttlege, discuss how he became involved with this company, and how he turned it around. In the picture above, you will see a blue neon sign in the background that says, “Take Action.” It’s kind of hard to see. However, as I left, that phrase stuck in my head.
The Key
They key to process improvement is to understand when to Take Action. If you are a company that embraces continuous improvement, then “Take Action” is as natural as breathing. If your company does not have a strong commitment to continuous improvement, you will need to determine the best way to justify your ongoing efforts.
Theory of Constraints - The Actions You Take
I was also recently introduced to the Theory of Constraints (TOC), and found it to be a relevant methodology to solving manufacturing issues. Combining the thoughts around “take action” and the Theory of Constraints lead me to combining the two. Below is the practical application of “Take Action” and TOC.
Phase 1: Identify the Constraint
The first step in TOC is to locate the constraint within the manufacturing process. This bottleneck is the weakest link that limits overall production capacity. Identifying it involves analyzing production data and flow.
Take the following actions:
- Analyze key performance metrics such as production rates, cycle times, and work-in-progress to find inefficiencies.
- Observe the production floor to detect delays or accumulations of work at specific stages.
- Consult with production staff to gather insights about potential bottlenecks.
Phase 2: Exploit the Constraint
Once identified, the next phase is to optimize the constraint's performance. This means ensuring the bottleneck operates at maximum efficiency without interruptions.
Take the following actions:
- Prioritize tasks to ensure the constraint is always engaged in value-added activities.
- Minimize downtime by maintaining equipment and providing necessary resources.
- Implement process improvements to enhance throughput at the constraint.
Phase 3: Subordinate Everything Else
Align all other processes to support the constraint. This ensures that the rest of the production flow operates in harmony with the bottleneck.
Take the following actions:
- Adjust production schedules to match the pace of the constraint.
- Streamline workflows to prevent overproduction ahead of the bottleneck.
- Ensure timely delivery of materials and inputs to the constraint.
Phase 4: Elevate the Constraint
If the constraint's capacity remains insufficient, consider making significant changes to elevate its performance, such as investing in new equipment or processes.
Take the following actions:
- Expand capacity by adding shifts or machines.
- Introduce new technologies or methods to increase throughput.
- Train staff to enhance their skills and efficiency at the bottleneck.
Phase 5: Repeat the Process
Once a constraint is resolved, another may emerge. Continuously apply the TOC process to identify and address new bottlenecks.
Take the following actions:
- Regularly review production data to spot emerging constraints.
- Maintain a culture of continuous improvement and adaptability.
Take Action Now
Whether you use TOC, Six Sigma, Lean, Toyota Production System or some hybrid surrounding these methodologies, Take Action dictates that you try something. MTG can help you decide the best action to take in order for you to meet your goals.
What can MTG do to help you improve your operations?