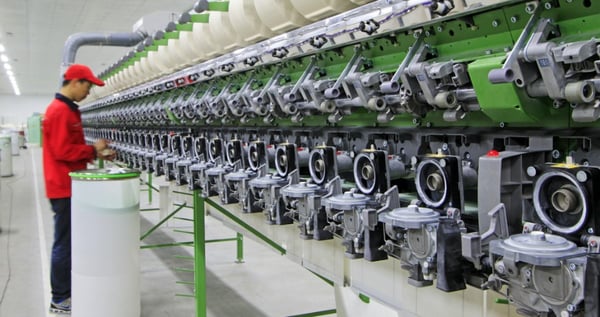
David Collins explains how a factory can use simple statistical process control tools such as a control chart to detect variations, take action, and reduce quality problems.
TRANSCRIPT
Every process, every manufacturing process, everything has some form of variation to it. How you control that variation is a good way to know how successful you’re going to be in your overall manufacturing process.
When you’re putting parts together, when you’re getting parts from other suppliers, outside suppliers that are coming in to put together, when you’re working with machinery, everything has some small variation to it. When all the different variations are added up, it could equal disaster to the product or a very bad product.
Controlling that variation using statistical process control is a great way to understand the variation and to be able to use it to your benefit so that the people manufacturing your product will manufacture it the right way all the time.
And statistical process control isn’t complicated, it’s very simple. It can be done by hand; it can be done at different job stations. All you have to do is get some charts up, start tracking data that’s coming down the line, maybe with some process control use a little bit of math formulas to determine if the process is in control or not. And then, as you understand the variation and you see the variation occur, you find ways to reduce the variation. Until you know what that variation is you can’t find ways to reduce it. So just charting alone can help you an awful lot.
And again, charting is basically free. A piece of paper, a pencil up by the job station, and every time something comes across and is measured in some way, that dot is put on the chart or that number is written down.
Doing this is simple. After a short amount of time, maybe one or two shifts, you’ll start to see variation and you’ll start to understand some of the ways that it’s affecting you. And once you see the ways it’s affecting you, you’ll go back into your process and you’ll start to work on ways to fix it. Some ways to fix it might be as simple as updating the SOP and making it harder for the person to make that mistake that causes variation. Maybe it’s doing preventative/predictive maintenance to cause less variation to machines. (Remember, if you’re not doing your maintenance your machines will have a lot of variation and that variation will cause scrap, and scrap is just money you’re throwing out the door.)
Statistical process control will help you reduce scrap. Statistical process control will help you improve your first time run so you don’t have a lot of repairmen doing work that they don’t need to do. Repairmen are costly. And really, even when you repair something, that’s never as good as it can be when you run it the first time.
Lastly statistical process control, of course, can be used with computers. Good statistical process software is available. Again, it’s not very expensive but it is useful and very usable and it will help your engineers to do better analysis of the problems and what the issues are and then go back into the process and fix it.
I’m a big believer in statistical process control. You’ll hear some buzz words like Six Sigma, CP, CPK, the mean, the spec limits, things like that. Again, very easy to teach, very easy to get in place. It’s something that somebody could help you with and you could get in place really within two, three days of learning how to use it. It’s a real simple process and then using it can help your company to become a much better manufacturer, with higher quality and lower cost.