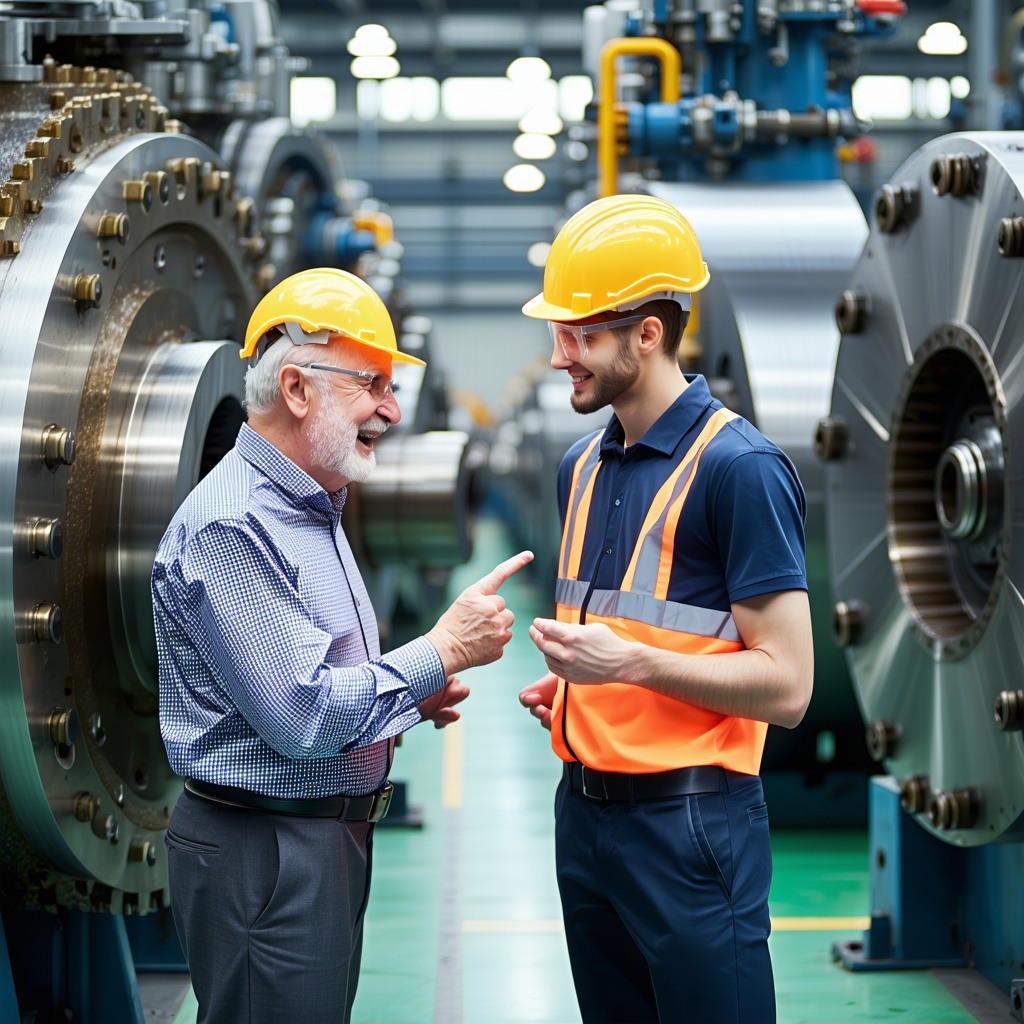
The average tenure of a front line worker continues to move become smaller . People used to hold factory line jobs for 10+ years are now changing roles often. Low unemployment within the labor sector is one of the biggest issues that employers face, which directly affects factory productivity.
In addition, experienced staff continue to retire. Baby boomers, which possess significant institutional knowledge are leaving the workforce in droves.
Combining an emerging transient workforce and an organization’s knowledge retiring, knowledge transfer becomes a critical manufacturing capability. The ROI of institutional knowledge transfer programs is pretty easy to measure:
- Productivity – By having programs that get staff up to speed faster, productivity does not take a hit with a new hire.
- Turnover – There is enough evidence that shows that investing in these programs reduces turnover.
- Employee satisfaction – Employees that can help others are more likely to be happier employees, which is related to reduced turnover.
The ideas below provide some insights into different approaches to improving internal knowledge transfer.
Where AI Visual Inspection Makes Sense
Mentorship Programs
Establishing mentorship programs pairs seasoned staff with newer hires, creating opportunities for hands-on learning and guidance. Mentors can share their experiences and insights, ensuring that critical knowledge stays on the shop floor.
Most senior employees are eager to share their knowledge and experience with newer employees but often lack the structure to do so. Creating a mentorship program requires leader ship support and recognition. A good place to start is by setting aside time for the mentor and employees to meet on a weekly or bi-weekly basis. Mentors should be recognized by the organization for their contributions. A simple reward and award goes a long way to motivate people to become involved.Work Instructions / Standard Operating Procedures
Documenting processes, procedures, and best practices in detailed SOPs provides a reference point for all employees. These documents should be regularly updated to reflect any changes in operations or technology. If you don’t have these in place, the cost of training a new hire becomes more expensive, as it takes more time to get your staff up to speed and potentially impacts productivity and output.
Many readers may be shocked to see how many companies still do not have good work instructions or any at all. Work instructions that represent the actual work experiences, rather than an idealized version. Having an experienced employee develop the work instructions will ensure that they are as close as possible to real life operations.
Training Sessions and Workshops
Regular training sessions and workshops help employees stay abreast of new techniques, tools, and technologies. These can be conducted in-house or through external providers and should be designed to cater to different learning styles.
Cross-Training
Encouraging cross-training allows employees to learn multiple roles and processes. This not only enhances their skills but also ensures that knowledge is distributed across the workforce, reducing dependency on a few key individuals. Most employees are interested in learning more than one skill. Rewards should be provided for staff that can effectively perform multiple roles within a manufacturing operation.
Cross-training can be difficult at times as the tight labor market means that companies often do not feel they can spare the staff to work on a task that they are less skilled at. While that is understandable, cross training is valuable for moral and risk aversion. It is a good idea to cross train at almost all levels. MTG crossed trained all supervisors at a client's factory in Eastern Europe. In the end, the factory had strong coverage across the entire organization and it each supervisor was able to contribute to their cohorts efforts.
Feedback and Continuous Improvement
Creating a culture of feedback and continuous improvement encourages employees to share their insights and experiences. Regularly soliciting feedback on processes and practices can lead to valuable enhancements and innovations. As a part of your continuous improvement investment, the realized savings could be awarded to the employee or team for their work.
Knowledge Transfer is Vital for Future Operations
Effective knowledge transfer on the shop floor is essential to sustaining a manufacturing organization’s productivity and competitiveness. By implementing strategies such as mentorship programs, SOPs, training sessions, and leveraging technology, companies can ensure that valuable institutional knowledge is preserved and passed on to future generations of workers.
What can MTG do to help you improve your operations?