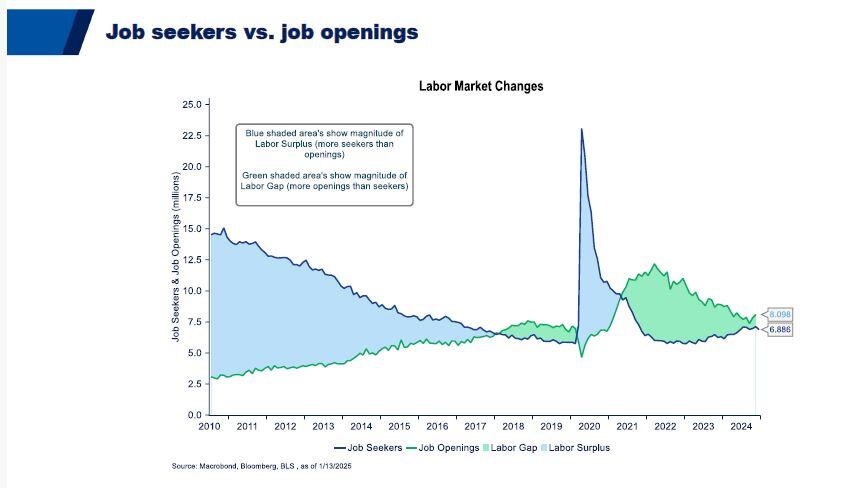
A recent economic survey provided by 5/3 Bank at the ACG Chicago annual middle market forecast event provided some insight into current labor conditions. The tight labor market within manufacturing continues to be a top five issue for manufacturing operations leadership. The graph below provides some insight into the imbalance between jobs and the labor market to fill those jobs. The green is the difference.
If labor continues to be an issue, here are four different strategies that may help you ensure that you have addressed labor availability as well as labor safety.
Implementing Automation and Robotics
Depending on your company’s propensity to invest in automation, this can provide significant labor savings. Automation can also improved first pass yield and quality. For repetitive tasks, Automation and robotics reduces labor costs for a given product, allowing workers to focus on complex activities. A study by the International Federation of Robotics (IFR) shows that automation can increase productivity by up to 30% and reduce labor costs by 20%. [Source: IFR]
Potential Savings
- Increased Productivity: Up to 30%
- Labor Cost Reduction: 20%
Adopting Lean Manufacturing Principles
If you have not begun your lean journey, this might be the right time. Lean manufacturing focuses on eliminating waste and optimizing processes. According to the Lean Enterprise Institute, companies can achieve a 25% reduction in manufacturing costs by implementing lean principles. [Source: Lean Enterprise Institute]
Potential Savings
- Cost Reduction: 25%
Enhancing Workforce Training and Development
Skilling up your workforce is always good. It demonstrates investment in your team, and can potentially reduce turnover, which can be a big expense for any labor intensive industries. Research from the Association for Talent Development (ATD) indicates that companies investing in training see a 24% higher profit margin. [Source: ATD]
Potential Savings
- Profit Margin Increase: 24%
Implementing Ergonomics and Workplace Design
Similar to investing in training, investing in the workforce environment results in cost avoidance. It also demonstrates to your staff that you care about your staff, ultimately reducing turnover. The Occupational Safety and Health Administration (OSHA) states that ergonomic improvements can lead to a 58% reduction in musculoskeletal disorders. [Source: OSHA]
Potential Savings
- Reduction in Musculoskeletal Disorders: 58%
Implementing these strategies can significantly reduce labor effort, enhance productivity, and ensure a safer work environment.
Conclusion
While labor availability will continue to be a challenge for organizations, investing in your workforce and automation ultimately improves your ability to drive down labor costs.
What can MTG do to help you improve your operations?