Vietnam Manufacturing Consultants
Improve Your Manufacturing Operations in Vietnam
Collaborate with our local experts to refine processes, reduce inventory, and cut costs across your Vietnamese facilities.
Experienced Factory Management & Technical Consultants Based in Vietnam
Our team in Vietnam consists of seasoned manufacturing veterans. Directly from your factory floor to the executive suite, we resolve challenges and create strategies for sustainable advancement in your operations.
Our Manufacturing Consultancy Services
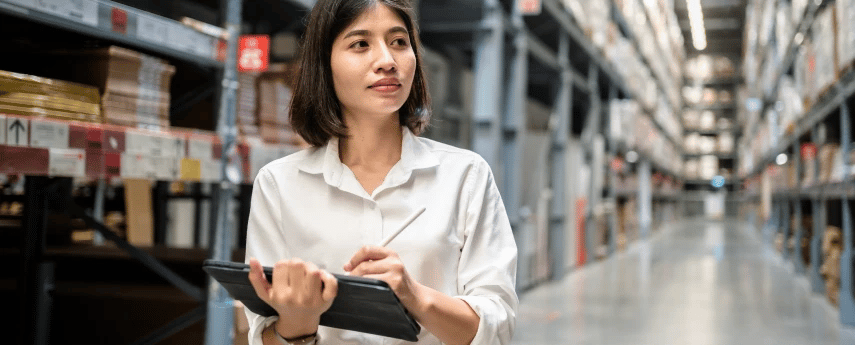
Optimize your Vietnam manufacturing operations with our detailed assessments. We conduct in-depth evaluations of your processes, management, and layouts, moving beyond basic audits to identify fundamental issues.
Transitioning manufacturing out of China to Vietnam? Our factory setup services streamline your shift, guiding you from site selection in Vietnam's dynamic manufacturing zones to launching operations, ensuring a seamless establishment of your manufacturing base.
.webp?width=855&height=345&name=Rectangle%2016%20(1).webp)
MTG's approach to factory turnaround in Vietnam focuses on strategic change management, resolving operational problems, and providing ongoing support for continuous improvement. We ensure that your manufacturing transitions are not only effective but also maintainable over the long term.
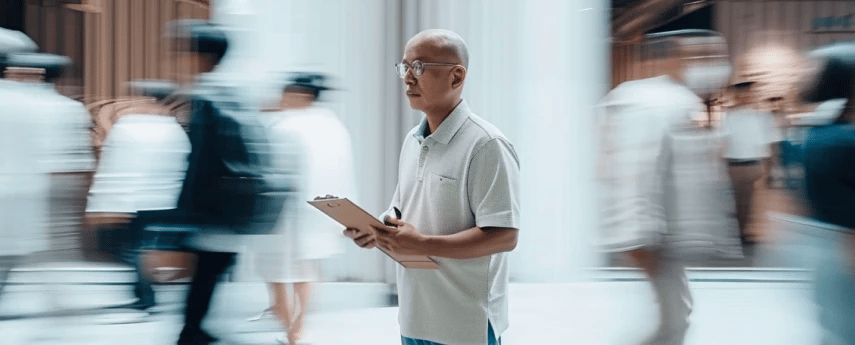
MTG's specialists have successfully improved manufacturing outcomes (lower costs, faster delivery, higher quality) across a wide variety of industries and locations.
Our proven approach using lean manufacturing, six sigma, and decades of experience will achieve the quickest results for your factories in Vietnam.
Successful Manufacturing Transformation in Vietnam
We typically work on engagements of 3-12 months with our consultants at your facility several days a week. Our engagement managers provide guidance, and our technical consultants provide the type of assistance necessary to reach your objectives.
Enhancing Production Efficiency For a US-Based Window Manufacturer
N/A
- Increased annual revenue by $2 million.
- Increased daily production value by $6,000+.
- Boosted OEE from 40% to 83%.
- Reduced headcount, achieved up to 40% improvement in production output.
- Improved cash flow by $50,000+ per month by reducing inventory and Work in Progress (WIP).
Where We Help You On-Site
Our consulting services cover a wide range of factory operations and processes.
Process Control
We focus on improving productivity at your facility and preventing human error, with tools like line rebalancing, poka-yoke, process improvement, and more.
Removing Bottlenecks
We use logistical and process changes, operator training, and self-inspection, among other tools, to achieve continuous flow production.
Quick Results
We aim to maximize benefit in a condensed timeframe by determining high impact improvements.
Standardized Workflow
We help companies analyze their entire workflow to identify opportunities to improve efficiency by implementing standard operating procedures and training staff for sustained improvements.
Mistake Proofing
As ‘inventory’ and ‘defects’ are less detectable in technical processes, productivity can often be a significant issue. We help improve this through changes in logistics, mistake-proofing, and other tools.
Improved Productivity
We focus on developing a process improvement plan for a system with reduced cycle time and higher productivity by addressing procedural, data transparency, and cooperation issues.