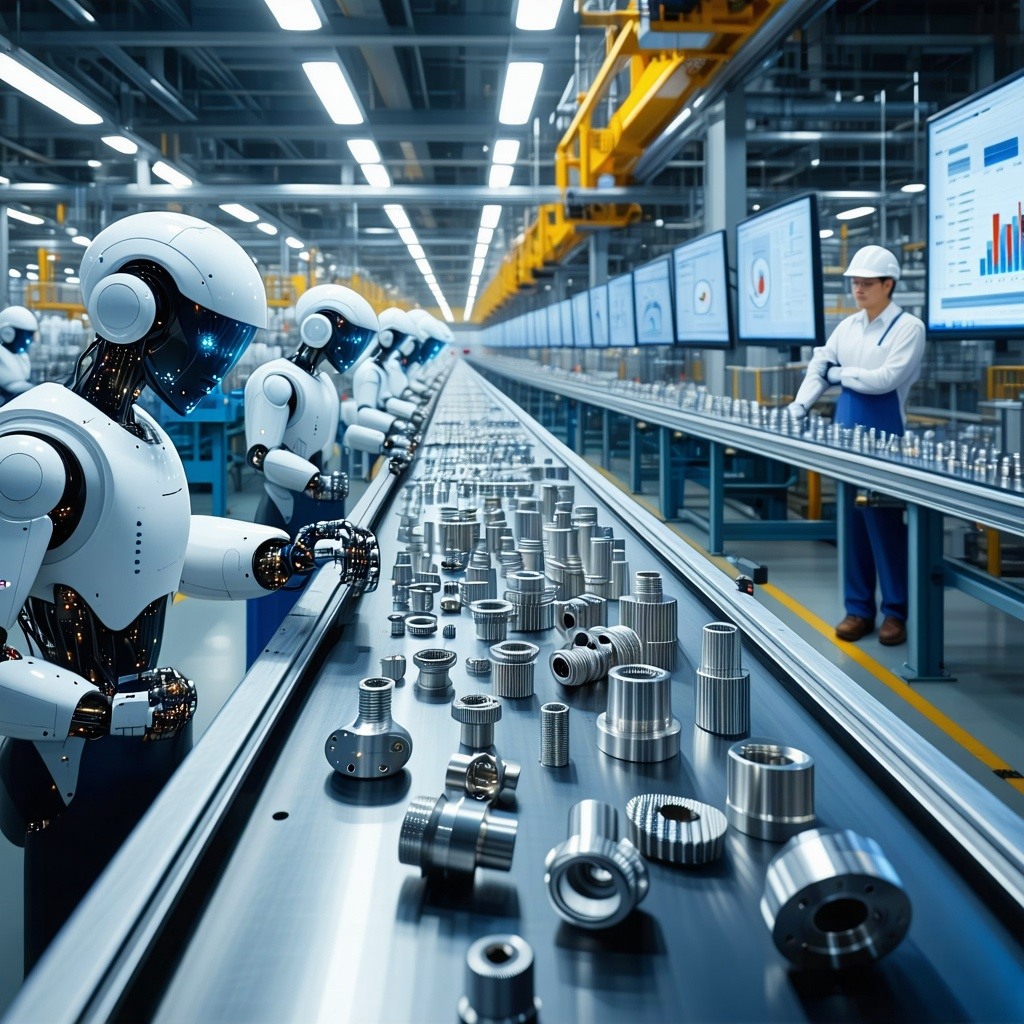
AI driven visual inspection adoption continues to grow across multiple manufacturing verticals around the world. When comparing AI inspection to human based monitoring, the features are pretty clear. The AI system is not subject to human error, and is not affected by lack of caffeine, outside personal issues or being late to the shift.
However, while AI visual inspection systems hold great promise, they also have their limitations. This blog post explores the capabilities and constraints of AI visual inspection, delineating AI’s strengths as well as areas where AI may need some help.
MTG has recently started integrating AI driven visual inspection tools with our manufacturing transformation clients. These powerful tools provide amazing opportunities to change manufacturing operations. However, treating it as an all-one-solution can be more damaging than helpful to manufacturers.
Where AI Visual Inspection Makes Sense
High-Speed and High-Volume Inspection
AI visual inspection systems can process and analyze large volumes of images quickly. They enable manufacturers to inspect thousands of parts per minute, ensuring that production lines run smoothly without bottlenecks. The benefits include:
- Consistency: AI systems maintain a consistent level of accuracy and precision throughout the inspection process, avoiding fatigue and human error.
- Scalability: AI systems can be easily scaled to match increased production demands.
Defect Detection
Similar to inspection, AI visual inspection excels at identifying defects in manufactured products, such as scratches, dents, discoloration, and misalignments. With machine learning algorithms, these systems can be trained to recognize a wide array of defects.
AI can detect complex patterns and anomalies that might be missed by the human eye, and can then be incorporated into the visual inspection capability. Through this continuous learning, AI systems improve their accuracy over time by adapting to new defect types.
Efficiency and Cost-Effectiveness
AI visual inspection reduces the need for manual labor, leading to substantial cost savings. Moreover, it minimizes the risk of human error, thereby reducing waste and rework.
Lower dependence on human inspectors allows for a leaner workforce and reduces operational costs. It also allows for human resources to focus on other tasks with a greater value add to the manufacturing process.
Where AI Visual Inspection Needs Help
Complexity and Customization Requirements
AI visual inspection systems struggle with highly customized products that have unique features and specifications. These systems require extensive training and fine-tuning to handle such complexity. These systems require significant amounts of training data to ensure the system can accurately identify defects.
Environmental Factors
AI visual inspection systems can be sensitive to changes in environmental conditions such as lighting, temperature, and cleanliness. These factors impact the accuracy of the inspections. Specifically, fluctuations in lighting can affect the system's ability to detect defects, which may require significant investments in lighting on the shop floor.
Human Expertise and Intuition
Despite their advanced capabilities, AI systems lack the intuition and judgment that experienced human inspectors bring to the table. There are scenarios where human expertise is crucial.
- Complex Judgments: AI systems may not be able to make nuanced decisions based on incomplete or unclear data.
- Unpredictable Defects: Human inspectors can recognize and adapt to unexpected defect types that AI systems may not be trained for.
Finding Errors Not Solving Problems
AI inspection capabilities are good at finding defects and errors but cannot be used to get to the root cause. That requires human expertise and follow through. You cannot inspect yourself to good quality. Relying on AI inspection as the complete solution is an ineffective problem solving methodology.
What Should a Manufacturer Do?
Manufacturers must carefully assess their environment and production requirements to determine where AI driven visual inspection can be optimally applied and where human intervention remains necessary. Some of these systems have a relatively low risk of failure because of the nature of the project. The larger the project, the more time should be spent determining the financials of this investment.
Balancing the strengths of AI with the expertise of continuous improvement professionals ensures a robust and efficient inspection process that upholds the highest standards of quality.
What can MTG do to help you improve your operations?