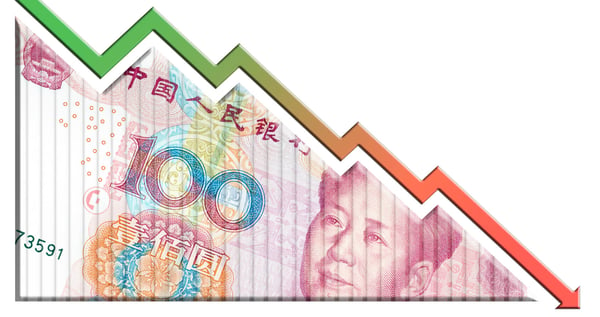
Are you tired of the general inflation in raw material prices, wages, and other costs that impact manufacturing in China? And, as a buyer, are you afraid your margin will keep eroding if prices of finished goods keep rising?
There are basically two ways to contain the China manufacturing cost – working on reducing waste in existing processes, and automating manual processes. Keep this in mind when planning supplier development efforts that make sense for your company.
1. Lean Manufacturing Techniques + Staff Engagement
This is a wide topic. And many things that don’t seem to impact cost end up having a high impact on the bottom line. As Shingo wrote, “there are four purposes of improvement: easier, better, faster, and cheaper. These four goals appear in the order of priority.”
Let’s break it down in 3 complementary approaches, from the perspective of what factory management can do.
a) Industrial engineering work
In a previous article we listed 7 industrial engineering applications that increase labor productivity:
- Making products flow by avoiding queues in front of bottlenecks and avoiding the habit of processing by batch where it is not necessary
- Reducing inventory, and especially work-in-process inventory (located in production workshops)
- Separating logistics work (bringing the components and presenting them the right way) and manufacturing work (transforming the components)
- Presenting materials and tools at point of use – for example, not having to go to another location to fetch parts
- Writing good work instructions for operators, and involving them in that process
- Semi-automating manual processes and/or using sensors to detect problems
b) Quality engineering work
This article is about cost, so why bring up quality?
Well, there are two reasons for this.
First, the costs of poor quality often represent more than 10% of a factory’s total costs. That’s a lot of money!! By reducing the need to reprocess products, to scrap materials (which may have been fully processed), and the need to compensate unhappy customers, the factory can achieve serious savings.
Second, quality improvement initiatives can lead to ideas that reduce costs significantly through process upgrade.
c) Staff engagement for bottom-up improvements
There is only so much cost-cutting that can be done when managers say “change this, change that”. Who really knows the day-to-day operations, the challenges (big and small), the behaviors that make no sense, etc.? The staff who works on the floor!
Watch this video and you will have an idea of the way it can work.
2. Automation of Processes in Order To Save on Labor Costs
There are basically 4 ways an automated production system cuts costs, when it is implemented properly.
a) Fewer people means lower total wages
In some cases, the fully-loaded cost of automated equipment, over its expected lifetime, is 2 to 3 times lower than the wages and social security contributions of the workers (including production operators, but also logistical operators if they are not needed by the new process).
If the automated equipment collects data, issues alerts, and pushes the few pieces of information the ERP needs, there is also less need for indirect workers.
b) Lower overhead costs
Fewer direct workers and fewer quality staff means less management. When an operator quits and a new one is hired, there are a lot of hidden costs – they amount to about 25% of that operator’s salary because of lower productivity, worse quality, training needs, the job of hiring, etc.
When one adds the dormitory, the canteen, the costs of accidents and suicides, and so on, to the equation, one realizes that labor-related costs are not negligible!
c) Lower costs of poor quality
How many times have you heard a factory rep saying ‘there will always be defects, since this is a manual operation’? It is true that good mistake-proofing, visual guides, and other smart engineering solutions can prevent most manual mistakes, but we see very few of them in Chinese factories.
In contrast, a machine that follows the jidoka principle of stopping when an error is detected will create much fewer defects – as long as it is properly programmed and maintained. And lower defects lead directly to lower costs!
d) Finding the right customers is easier
Once you have done the big move to automation and the hard work to make it work smoothly, you are no longer one interchangeable factory among hundreds of others. Some buyers are looking specifically for manufacturers like you.
Do you still need to attend trade shows, pay for being listed on B2B directories, and so on? Maybe not. If you target a handful of large companies that buy in your industry, a more targeted sales approach might be sufficient.
We find that more and more China manufacturers go for ‘shiny objects’ (automation), but few do the hard work of improving their processes with good old methods.
One common issue is that, instead of first planning how to improve their processes, and then coming up with automation where needed to support the process improvement plan, they go directly toward automation. They call equipment manufacturers and get a catalogue first, rather than starting with a holistic analysis of their situation and what could be done.
Have you observed the same misguided approach to cost cutting? Share your stories and experiences with us, we'd love to hear from you!