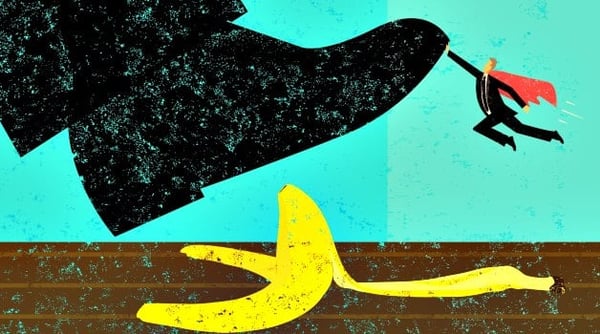
Together with staff training, mistake proofing manufacturing by performing specific prevention activities is key to factories who seek to reduce their quality issues. Keep reading as CMC explore mistake proofing in China in more detail...
Mistake Proofing Manufacturing In China
Unfortunately, the concept of prevention – doing some extra work now in order to reap larger rewards in the future – is still foreign to most Chinese people. This is not only an issue caused by short-term thinking. It also seems they have difficulty believing in a theory about how things work in their operations.
1. Common misconceptions of Chinese managers
When we ask Chinese factory managers about the cause of their quality problems, they usually give us these answers:
- The workers don’t pay attention to what they do, and they make mistakes.
- Ideally we would only have machines rather than people. Machines don’t make mistakes.
These answers are wrong at several levels:
- Bad management demotivates workers, which is why they may not be very invested in their jobs.
- Good process engineering removes opportunities for human mistakes. If this preparation is not done right, production operators are victims of their process and can’t help making mistakes from time to time.
- Machines can cause very costly quality issues very fast, before anyone could see it and stop the process. If setups and maintenance are not done right, automated equipment can drive a factory out of business.
2. Mistake proofing manufacturing operations done by hand
The best mistake-proofing devices do two things:
- They make the operation impossible if there is a mistake;
- They don’t add any work (this way they will always be in place, even when production has to be rushed).
Here is an example coming from the book “Poka Yoke”.
The guide pins have different sizes, to ensure a piece is always presented in the right direction.
There are many kinds of mistake-proofing devices and systems. With the development of ever-cheaper and ever-better-connected sensors, possibilities are expanding quickly.
Some less ambitious solutions, such as color-coding cables and the matching ports, can reduce the occurrence of quality issues. They don’t qualify as “mistake proofing” but as “mistake reducing” and can often be implemented in a very inexpensive manner.
3. Preventative and predictive maintenance: a way to mistake-proof your equipment
Do you wait until your equipment breaks down, and then call your maintenance specialist to repair it? Before breaking down, the equipment might have produced a lot of bad pieces.
For example, a machining tool might have been used and damaged for a few weeks before breaking. In addition to quality issues, poor maintenance costs a lot of money through lost production since a machine might be down for several days.
To avoid this, you can apply a combination of two types of maintenance:
- Preventative maintenance – having a plan to clean the machine, check the settings, check the condition of certain pieces, etc. on a regular schedule.
- Predictive maintenance – based on information from the equipment manufacturer and based on past failures, be ready to change certain parts of the equipment at certain dates.
Conclusion
As written above, these mistake proofing concepts are often foreign to the vast majority of Chinese manufacturers. They sincerely tell their customers that more inspection is the only way to achieve better quality results. They have never visited a factory with very few inspectors and a near-zero defect rate.
Fortunately, they tend to respond well to simple mistake-proofing devices. In their eyes, the more electronics (sensors, alarms…) that are incorporated, the better.
However, they don’t respond very well to maintenance programs. Most of them are convinced that machines are THE solution and they have a hard time accepting that they need to be taken care of and pampered carefully.
Where do you stand on mistake proofing manufacturing?
Is more inspection key to better quality in your opinion? What results have you had?
Please share your thoughts or questions with our community by leaving them as a comment below.