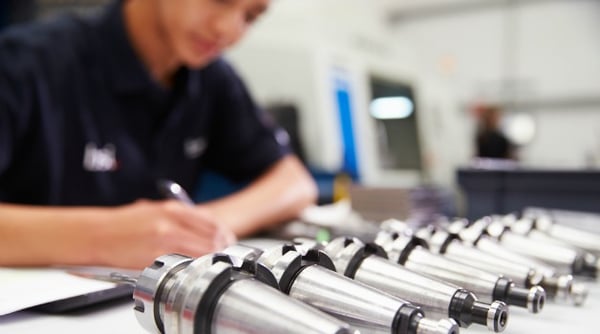
“Poor training” and “low employee motivation” are often root causes of serious issues. Every factory manager will agree that well-trained and motivated employees would save a lot of money to their organization.
But how to achieve this?
Manufacturing quality training for your Chinese operators is the solution you're looking for. Let's discuss it here...
Manufacturing Quality Training for Chinese Operators. A Must?
In China, very little is done in this area. It reminds us of a joke that goes as follows:
CEO: ‘Shouldn’t we train our employees?’
CFO: ‘But… what if they leave?’
CEO: ‘Well… what if they stay?’
In our daily observations, it seems the CFO’s narrow and short-term view has won over and over. And yet, it is not difficult to demonstrate that training employees is a wise choice from a return-on-investment perspective.
1. The case for manufacturing quality training
Most factories in China suffer from a staff turnover oscillating between 30% and 90% a year. It is quite costly – a departing production operator costs the company 2-3 months of her salary. Why? The company has to fill out paperwork, search and hire a replacement, provide basic training and extra supervision to the new employee. And the temporary loss in production numbers and in quality has a financial impact.
In contrast, a well-trained workforce can be engaged to work on improvements. As shown in this case study, it can lead to massive savings and sustain itself in the long term.
An engaged workforce feels respected, feels pride in what they have accomplish, and does not turn over. We have brought the turnover rates of some factories under 10% a year (including the New Year period).
2. Training production operators
The very basics every operator should know are:
- How to operate production equipment safely;
- How to do the work;
- How to recognize quality issues and what to do about them (for example, look at the graph below);
- Whom they can consult if they have a problem about their work;
- How the team’s output impacts the whole company’s performance (and how to read the performance charts that, hopefully, are placed on walls in their area);
- What is considered good behavior and will tend to lead to promotions and extra training in the future.
Ideally, they would be coached in to preparing work instructions such as this. More photos and drawings and less text is usually better.
3. Training leaders
Depending on the production organization and the size of the factory, there might be team leaders, group leaders, and/or supervisors. The terminology is not important. Responsibility for cost, efficiency, timing, and quality should be clearly assigned.
When it comes to managing quality, leaders need to work on two things:
- Making problems visible as fast as possible (for example checking the content of red boxes every 10 min for defective parts, writing findings on a dashboard…);
- Follow an appropriate procedure when addressing a problem (and not jumping to conclusions very fast).
It means they need a basic training in the problem resolution method. They can’t be left to operate with a “shotgun approach” where they do no planning, they have 5 ideas about the potential cause for a quality issue, they test each of these ideas one by one, and they never try to address a root cause.
Conclusion
To conclude, providing appropriate manufacturing quality training and having employees apply the concepts and tools they learned is a proven method for better staff retention and cost savings. As a bonus, it also has a strong impact on production quality too.
Do you have training in place for Chinese operators and management?
Does it follow the principles outlined in this post, or do you do things differently? If the latter, what do you do?
Please take a moment to share your ideas and questions as a comment below. Our experts and community members would love to discuss them with you.