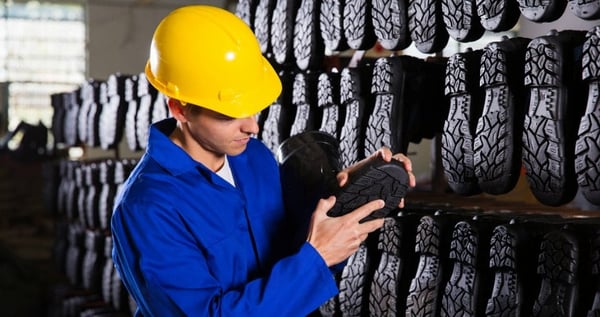
As we wrote in earlier articles, Chinese manufacturers are seldom aware of the full costs of external failures (when bad product is shipped out) and internal failures (when bad products iare stopped and dealt with before shipment). However, they are very aware of the costs of catching those failures.
In this case study, we will demonstrate the costs of quality when manufacturing in China...
1. Breakdown of the costs of manufacturing quality control
The factory boss can usually see what constitutes his labor costs. And he can see the costs of laboratory tests. When all the inspection and testing costs are put together, it might look like this:
The Chinese factory is aware that they will lose most of the customers if they ship their production without checking it. Therefore, they have built a quality department that consists of:
- 1 quality manager.
- 20 quality inspectors – some working on incoming materials, some checking production as it is ongoing, and some checking finished products.
- 50 operators are required to spend 10% of their time checking quality. In this case it means they take a little time to check the size and alignment of 1 out of every 5 pieces that go through their hands, in addition to their processing work.
- 5 quality technicians take the inspectors’ findings and input them manually into the IT system (admittedly, these efforts are pure waste and could easily be eliminated by equipping inspectors with tablets).
- 6 quality engineers have to work on the problems found by inspectors, and deal with the production department and/or with suppliers.
- Some certifications and/or tests in a laboratory add to those costs.
2. Justifying inspection & testing costs
As I wrote above, these costs are very visible to managers of a factory. Whenever a customer asks them to control quality more tightly, the Chinese manufacturer thinks “they want me to do more inspection & testing. It will increase our costs. We should increase their price.”
This steps from a misconception: “If we need to improve quality, we need to do more inspection”.
Quality guru W. Edward Deming rejected this idea:
“We cannot rely on mass inspection to improve quality, though there are times when 100 percent inspection is necessary. As Harold S. Dodge said many years ago, 'You cannot inspect quality into a product.' The quality is there or it isn't by the time it's inspected.”
So, how to improve quality? Through prevention activities. We will cover those in subsequent articles. But we should already point out that prevention alone is seldom sufficient to eliminate inspection & testing.
There is still a place for manufacturing quality control.
Catching a quality issue at the source and fixing it there is usually 10 times cheaper than letting it slip to the next stage in the process. In addition, catching a quality issue is the start of a correction & corrective action process which, in the long run, improves the organization’s systems and processes.
Conclusion
In summary, inspection and testing often add up to sizable costs for a factory. There are other ways to reduce those costs – for example setting up go/no go fixtures, mistake-proofing manual operations, following a plan for maintaining equipment, etc. These are all part of what we’ll call “preventive activities”.
Which preventative activities do you undertake to reduce the costs of quality?
Is manufacturing quality control something which gives you a headache at the moment? How, and why?
Please get in touch by leaving your thoughts and questions as a comment at the bottom of the post.