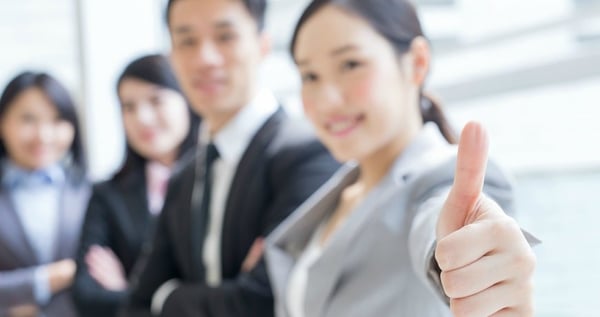
We just found an interesting discussion entitled "Corrective Action is not that complicated - why are we making it so difficult?" in ASQ's Linkedin group. It is particularly interesting for us working in the China manufacturing environment. Many people here just won't understand the need for corrective or preventive actions. Andrew MacPhee offered a simple, clear, and highly actionable approach:
For me it is a simple 3 step approach:
- Containment [or correction] - keep it away from the customer,
- Corrective Action - stop the same thing from happening to the same process again,
- Preventive Action - where else can I apply what I just learned?
It can actually be the basis for a problem resolution template. We found that, when you force people to fill out well thought forms, it guides their thinking and pushes them in the right direction. For a more in-depth explanation of the difference between Correction and Corrective Action, here is what Aaron Troschinetz suggests:
I think the designation for 'correction' vs 'corrective action' is important since 'correction' should always focus on 'What did you do specifically to correct (now) what I found?' while 'corrective action' should be taking you into your plan moving forward.'Correction' shouldn't be an exhaustive set of steps but rather the quick fix on an issue noted to 'stop the bleeding'. For instance, gage is found out of calibration; 'correction' is to calibrate the gage and ensure no product is affected.Now moving over to 'corrective action', assuming a solid root cause analysis is performed and driven down to a level of detail whereas it's clear what systemically is broken; 'corrective action' should be the plan to fix the process to avoid possible reoccurrence.Staying with the gage issue, the root cause could reveal a system that does not ensure appropriate processing of gages into a calibration area for 100% inspection; 'corrective action' could be the set of steps to re-design the process of receipt through calibration through returning the gage to its original point of use.
And, for a simple tool that can guide a manufacturer to find the root cause of a problem, please refer to this recent article.