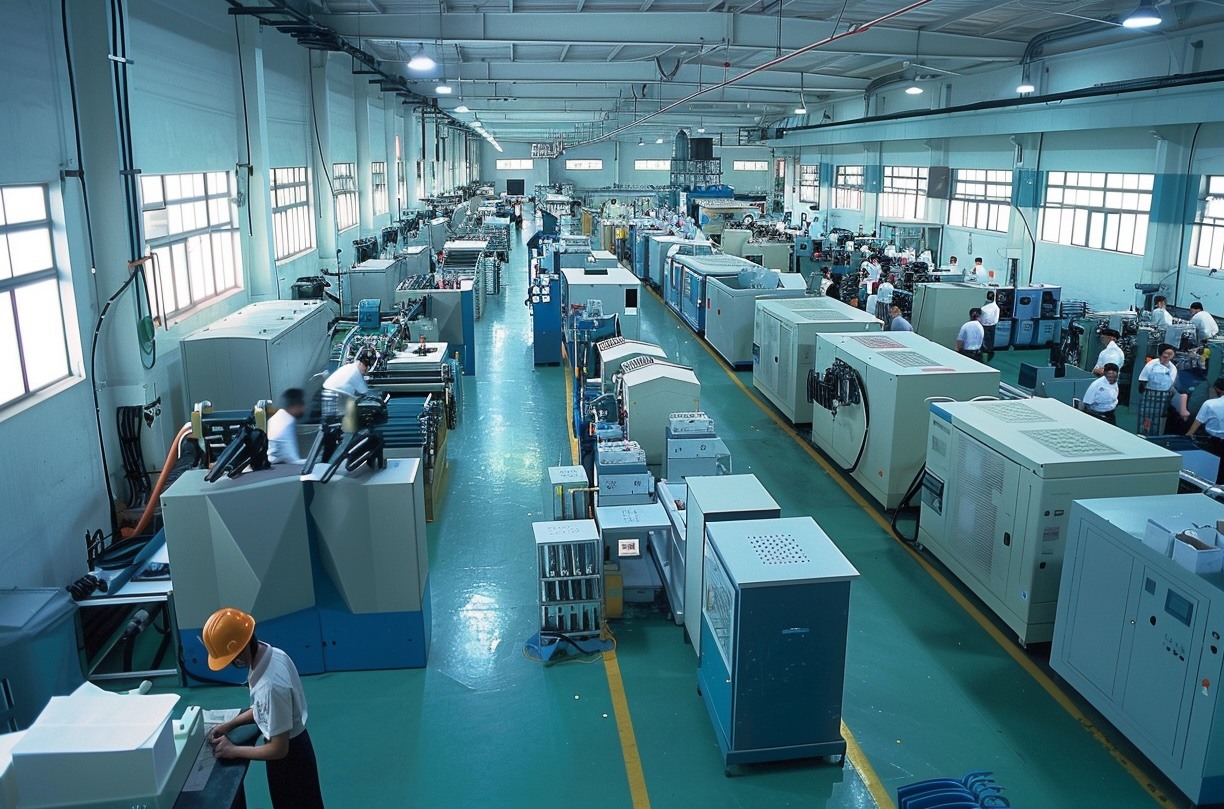
This is the 5th part of "How to Increase EBITDA in Manufacturing: A 6 Part Guide". If you'd like to view other posts in the series, the links are available on the right side menu of this post (desktop) or at the end (mobile).
Continuous improvement systematically seeks to achieve small, incremental changes through a variety of methodologies, including lean and six sigma practices. Manufacturers that embrace continuous improvement see waste reduction, operational efficiency, and improved product quality. Continuous improvement drives value to customers while simultaneously increasing profitability.
Implementing Lean Manufacturing
Widely adopted, lean manufacturing focuses on minimizing waste without sacrificing productivity. By identifying and eliminating non-value-adding activities, manufacturers can streamline operations and reduce costs.
Key Lean Tools:
- 5S Methodology: This involves sorting, setting in order, shining, standardizing, and sustaining a clean and organized workspace.
- Value Stream Mapping: This helps visualize the flow of materials and information required to bring a product to the customer, highlighting areas for improvement.
- Kaizen: A philosophy that encourages all employees to contribute to continuous improvement initiatives, fostering a culture of constant enhancement. Kaizen is the core of lean improvements. No improvement matters unless there is a culture in the company itself to implement the improvements and continue to iterate on them.
MTG incorporates all of these lean concepts in nearly every client engagement. We typically begin with a value stream map which provides insight into an improved and efficient production process. Here is a link that defines the different waste categories in Lean. Most companies are shocked to see how much waste exists in their operations. It is especially important as it helps the staff understand the need for change. Understanding how to identify and resolve these activities becomes a team effort, and a perfect opportunity for a team project.
Adopting Six Sigma
Six Sigma uses statistical methods to identify and remove the causes of defects and variability in manufacturing processes. The goal is to achieve near-perfection, with a defect rate of less than 3.4 per million opportunities.
Six Sigma Techniques:
- DMAIC: This stands for Define, Measure, Analyze, Improve, and Control. It’s a data-driven quality strategy used to improve processes. Click here to learn more about DMAIC.
- Root Cause Analysis: Identifying the underlying causes of defects to develop effective solutions. In some cases, finding root cause is obvious. In other cases, getting to root cause can involve a broad organizational group. Here is a guide to RCA.
- Control Charts: Monitoring process performance over time to ensure that improvements are sustained. These charts provide a rules driven, visual representation of trends within a manufacturing process, allowing you to identify conditions that cause “out of control” conditions. Here is a link to more information about control charts.
Investing in Workforce Training
A well-trained workforce drives successful continuous improvement outcomes. Once understood, lean/six sigma methodologies provide a decision making construct for continuous improvement project. We believe that effective implementation includes a combination of both classroom and hands-on activities that drive measurable outcomes.
Workforce Development Initiatives:
- Training Programs: Regularly scheduled training sessions on continuous improvement methodologies and tools.
- Employee Engagement: Encouraging a culture where employees at all levels feel valued and motivated to contribute to process improvement.
- Cross-Functional Teams: Creating teams that bring together diverse skills and perspectives to tackle improvement projects. Typically, these teams should meet on a regular basis (weekly) with a specific process or area to improve. Successful teams should be recognized and rewarded.
Leveraging Data and Analytics
Data-driven decision-making is at the heart of continuous improvement. By leveraging data and analytics, manufacturers can gain insights into their operations, identify trends, and make informed decisions.
Utilizing Data for Improvement:
- Real-Time Monitoring: Implementing IoT devices and sensors to monitor production processes in real-time and quickly address issues.
- Performance Metrics: Establishing key performance indicators (KPIs) to measure the effectiveness of improvement initiatives.
- Big Data Analytics: Using advanced analytics to process large volumes of data and uncover hidden patterns and opportunities for improvement. Many companies struggle with both what data to collect it, and then an efficient way to collect it. However, data collection is a critical part of any continuous improvement program since it becomes the basis for investments.
Fostering a Culture of Continuous Improvement
Finally, fostering a culture of continuous improvement is crucial for long-term success. This involves creating an environment where employees are encouraged and rewarded for identifying and implementing improvements.
Building the Right Culture:
- Leadership Commitment: Leaders that demonstrate a commitment to continuous improvement see better results. Few employees will follow a program that the leadership does not care about. There is no advantage for them. It was something that I learned as soldier: a leader’s role as much that of an example as it is someone who makes decisions.
- Recognition and Rewards: Acknowledging and rewarding employees for their contributions to process improvement. It can be as simple as a gift card and acknowledgement in front of the team at the morning production meeting.
- Open Communication: Promoting open communication and collaboration across all levels of the organization.
Continuous Improvement Strategies to Amplify EBITDA Gains
Increasing EBITDA in manufacturing through continuous improvement represents a multifaceted approach that requires commitment, strategy, and a willingness to embrace change. By implementing lean manufacturing and Six Sigma principles, enhancing operational efficiency, investing in workforce training, leveraging data, and fostering a culture of continuous improvement, manufacturers can achieve significant gains in profitability and sustained long-term growth.
What are your thoughts on leveraging automation to increase EBITDA. Let us know in the comment section below.