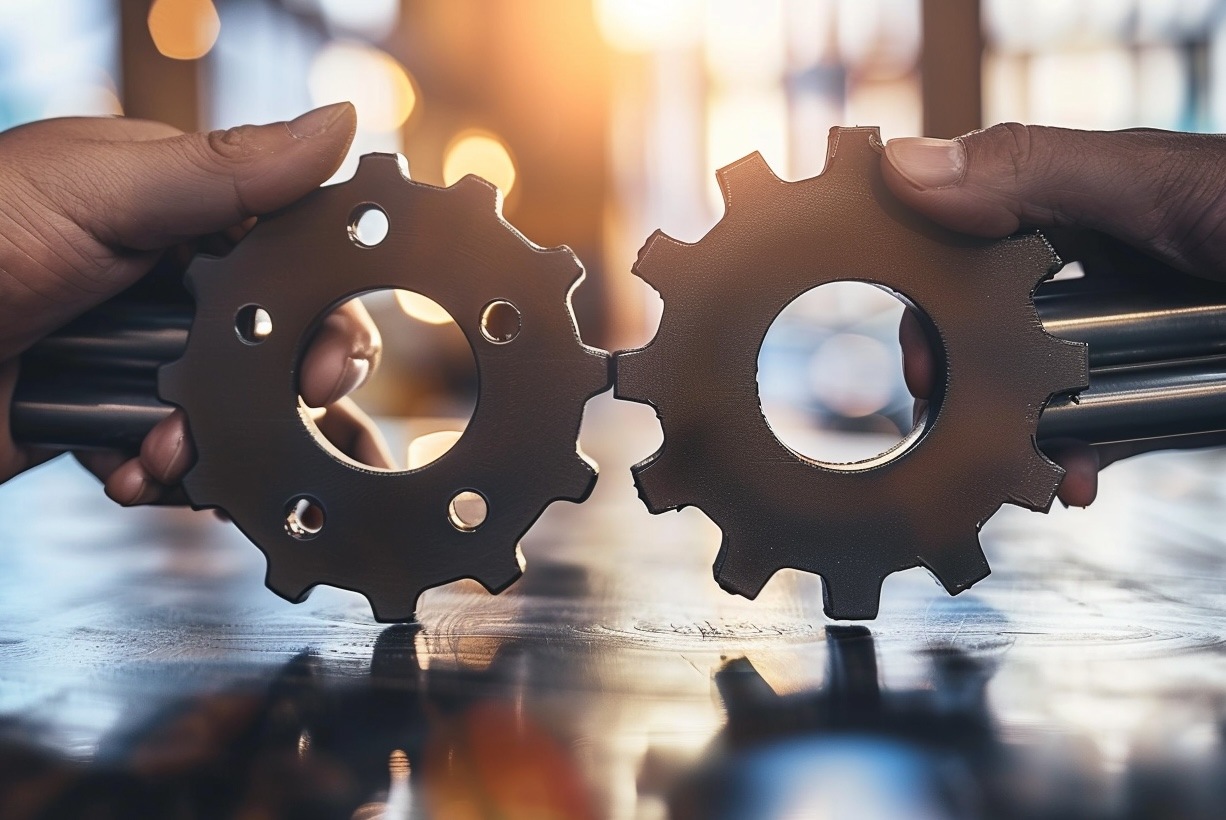
This is the 5th part of "How to Increase EBITDA in Manufacturing: A 6 Part Guide". If you'd like to view other posts in the series, the links are available on the right side menu of this post (desktop) or at the end (mobile).
One of the most effective strategies to achieve EBITDA growth is through fostering cross-functional collaboration. By leveraging diverse skills and perspectives across different departments, manufacturers can drive innovation, enhance efficiency, and ultimately boost their bottom line.
Cross-functional collaboration achieves impressive results and helps boost team morale, as indicated in this Forbes article.
Understanding Cross-Functional Collaboration
Cross-functional collaboration involves bringing together individuals from various departments—such as engineering, production, quality control, and supply chain—to work on common goals. This approach breaks down silos, promotes knowledge sharing, and fosters a more holistic view of manufacturing processes. The closer the individuals are to the problem, the better they usually are for solving the problem.
Building Cross-Functional Collaboration Skills
For cross-functional collaboration to be effective, team members need to develop specific skills. These include:
- Communication: Clear and open communication is crucial. Team members must be able to articulate their ideas, listen to others, and engage in constructive dialogue. A good way to encourage communication is to encourage active listening.
- Problem-Solving: The ability to analyze issues from multiple perspectives and develop innovative solutions is essential. Most people can be a problem solver with a little training in root cause analyze and motivation. This course from Invensis Learning provides insight into Root Cause Analysis:
-
Adaptability: Manufacturing environments are dynamic. Team members need to be flexible and adaptable to change. Adaptable people are often likely to be problem solvers.
-
Conflict Resolution: Diverse teams may face conflicts. Effective conflict resolution skills ensure that disagreements are managed constructively.
Managers and other employees are likely to know most of the people that have these skills. Choosing someone for a cross-functional team should be a prestigious appointment. A small reward and factory wide acknowledgement of an achievement is all the motivation needed.
Forming Cross-Functional Collaboration Teams
Creating effective cross-functional collaboration teams involves careful planning and strategic implementation. Here are key steps to form these teams:- Define Clear Objectives: Clearly outline the team’s goals and objectives. Whether it’s improving a production process, reducing waste, or enhancing product quality, having a clear focus is essential. The objective should be clear but not so hyper focused as it prevents people from being creative in their solutions. (maybe introduce the concept of SMART goals).
- Select Diverse Members: Choose team members with diverse skills and backgrounds. This diversity will bring different perspectives and ideas to the table, driving innovation. The positions should be relevant, however.
- Establish Roles and Responsibilities: Clearly define the roles and responsibilities of each team member. This ensures accountability and prevents overlaps. Roles and responsibilities do not (and should not) be connected to their job. The most senior person is not necessarily the leader of the group.
- Provide Training: Equip team members with the necessary cross-functional collaboration skills. Training sessions on effective communication, problem-solving, and conflict resolution provide benefits not only to the team but to the other interactions that your staff have on a daily basis.
Benefits of Cross-Functional Collaboration in Manufacturing
Fostering cross-functional collaboration can significantly impact a manufacturing business’s EBITDA by:
- Enhancing Innovation: Diverse teams can generate more creative solutions and innovative ideas, leading to improved processes and products.
- Improving Efficiency: Collaboration helps identify inefficiencies and streamline processes. Teams can work together to eliminate bottlenecks and reduce waste.
- Increasing Agility: The cross-functional team approach is likely to solve challenges related to manufacturing shortfalls when changing to a new product or scaling production up or down than centrally directed mandates.
- Boosting Employee Engagement: Collaborative work environments tend to have higher employee engagement. When employees feel their contributions are valued, they are more motivated and productive. Other employees will strive to be on the next cross-functional team.
Implementing Cross-Functional Collaboration in Your Manufacturing Business
To successfully implement cross-functional collaboration, manufacturing businesses should:
- Start Small and Learn: Like most initiatives, start with a low risk project and take the lessons learned to begin scaling across the organization.
- Use Collaborative Tools: Leverage technology to facilitate collaboration. Tools such as project management software, communication platforms, and data analytics can enhance team coordination. That said, the best method to make sure people speak with each other in person and have the freedom to bounce ideas around.
- Measure and Adjust: Continuously monitor the performance of cross-functional collaboration teams. Use metrics to assess their impact on efficiency, innovation, and EBITDA. Be prepared to make adjustments as needed to optimize performance.
Increasing EBITDA in manufacturing through cross-functional collaboration is a multifaceted approach that requires commitment and strategic implementation. By building cross-functional collaboration skills and forming effective teams, manufacturers can drive innovation, enhance efficiency, and achieve significant gains in profitability. Embracing this collaborative approach can lead to sustained long-term growth and a more resilient manufacturing operation.