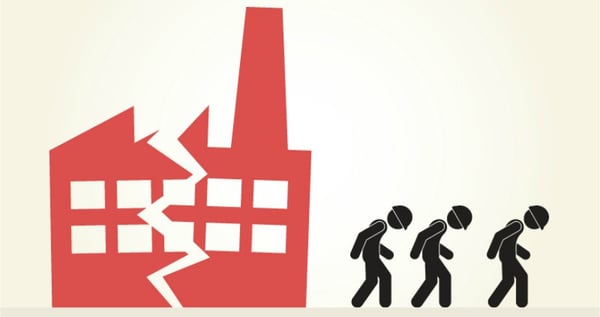
Plenty of management consultants, often calling themselves Lean consultants, work for Chinese factories. Unfortunately, their advice and systems don’t always steer the organization in the right direction.
Let’s study two of the major downsides to bad manufacturing management consulting which you should be vigilant to avoid...
1. The Focus on Paperwork
Here is a typical situation. To get ISO 9001 certified, a consultant is hired and delivers a pile of documents (a “quality management system”) that does not correspond to the company’s activity. It is not used in day-to-day operations, but it can be shown to external auditors.
What is the problem with this approach?
- It gives the wrong impression about standards – ISO 9001 doesn’t have to add work and look so boring.
- It teaches people how to cheat – the quality staff, who should always look for truth and make problems visible, is taught how to make fake records!
- It prevents the company from documenting its standards, since “we already have a quality management system”.
Yet, good Lean consultants will tell you that establishing standards (the best way we currently know of doing every important job) and helping people learn and apply them is a must. We are not advocating the need to document every single standard in wordy procedures, though. Here are a tips:
- The more graphical, the better. Many people don’t want to read long paragraphs of text.
- Whenever possible, design work aids that make it effortless to remember and follow standards.
- The absolute best is… to streamline a process and to eliminate certain steps that are deemed non-value-added. No need to document them!
- A nice-looking procedure is useless unless people actually comply with it. And this is more likely if the workers actually decided on the standard they would follow. This works well if they are given training and coaching. It is a very good basis for continuous improvement!
Another imperative is to maintain procedures and work instructions over time. The documentation is kept useful by avoid errors, contradictions, repetitions across several documents (which quickly lead to contradictions as changes are not applied to all documents), etc.
2. Lack of Prevention in Manufacturing Management Consulting Sessions
Most consultants ignore what we wrote before in The 5 Areas Your China Factory Turnaround Strategy Should Address.
Here are a few examples:
- They don’t push managers to put in place statistical process control where it makes sense.
- They don’t advocate preventative and/or predictive maintenance where it is most needed.
- They don’t propose to stop paying operators by the piece or to start giving them continuous improvement training.
- They don’t help with design for manufacturing when it comes to engineered products.
As a result, they have no impact on the company’s long-term performance.
In addition to paperwork, these consultants offer training sessions. They are commonly called “teacher” (‘laoshi’). But those training sessions don’t engage workers through workshops (for application of the concepts), and as a result they have very little impact.
Conclusion
To sum up, typical consultants help factories to trick external auditors and don’t focus management’s attention to what really moves the needle. This is bad manufacturing management consulting as it doesn't results in clear, long-lasting, factory improvements.
On the opposite, lean consultants are very light on paperwork and heavy on targeted improvement activities. They should have a logical plan for getting the organization to the next level, one change at a time.
Is your factory drowning in paperwork, or suffering from less than satisfactory management consultancy?
What kind of headaches is this causing?
Please feed back to us by leaving a question or comment below.