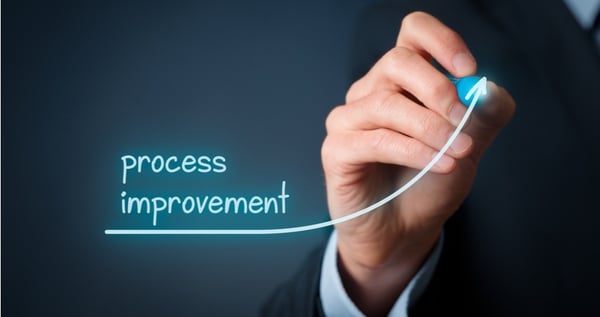
Many readers shared an article we published two weeks ago, Setting Up A Step-By-Step Process Improvement Plan In Your Factory, and we got some great feedback. By popular demand, we decided to dive deeper into this topic.
I recorded a 20-minute video that describes the improvement framework we follow.
It is based on the 11 steps shown below.
99% of Chinese factories follow no process improvement framework
Here is the approach we use at CMC. This is not something we often see in the companies we work with. In fact, if we exclude the factories that are part of a large multinational group, this type of approach is virtually non-existent.
The logic behind this framework
In this video I explain the logic behind the sequence of steps:
- Why the problem needs to be broken down as early as possible, in order to clarify the scope of the project.
- Why target(s) need to be set as soon as the scope is clarified.
- Why the team who will be involved in the improvement of processes needs to be involved in the problem analysis, root cause analysis, and comparison of action items.
- Why a target needs to be clear, specific, measurable, and time-bound.
- Why the success of the project needs to be evaluated all along the implementation phase, not after 3 or 6 months.
- Why a project team can’t just be disbanded, in the hope that the improvements will “stick” over the long term.
- Why a process improvement team is a great source of suggestions for other changes in the organization.
We provide many visual examples all along the video. It will give you a good idea of the way we work with our clients.
Click the button below to gain access to the FREE video, and listen to me talk you through the framework's benefits. You'll also be able to download it as a PDF for you to keep too:
Example of clear, specific, and measurable target
We use a variety of templates that facilitate analyses. Especially with the organization members.
Getting the team’s ideas and buy-in is critical. If consultants (or a few employees in a “kaizen office”) think up an action plan by themselves, its success likelihood will be much lower. There are two reasons for that:
- The people who know a process the best are those who work on it every day – not people who just observed it for a few hours. Get some input from the people closest to the process you want to improve!
- If you give a set of instructions to people, they may or may not cooperate. If they were involved in doing the diagnostic and in formulating the action plan, they are more likely to be motivated to contribute positively.
One example of team involvement is shown below.
Example of countermeasure evaluation
This format is great for writing down everybody’s suggestions and then scoring them based on their impact (--, -, +-, +, ++) and their benefit (cost, quality). Looking at many options is a proven method to get to better decisions.
Choosing the best countermeasures to apply to the problem becomes very easy and does not lead to heated discussions.
These are just two examples taken out of the video.
Take action to improve YOUR processes today
I will go over all these concepts in more detail, with plenty of examples.
So, if you are considering improving your processes, a good first step is to watch this 20-minute video. Just click the button below to get a no-commitment access to watch the video.