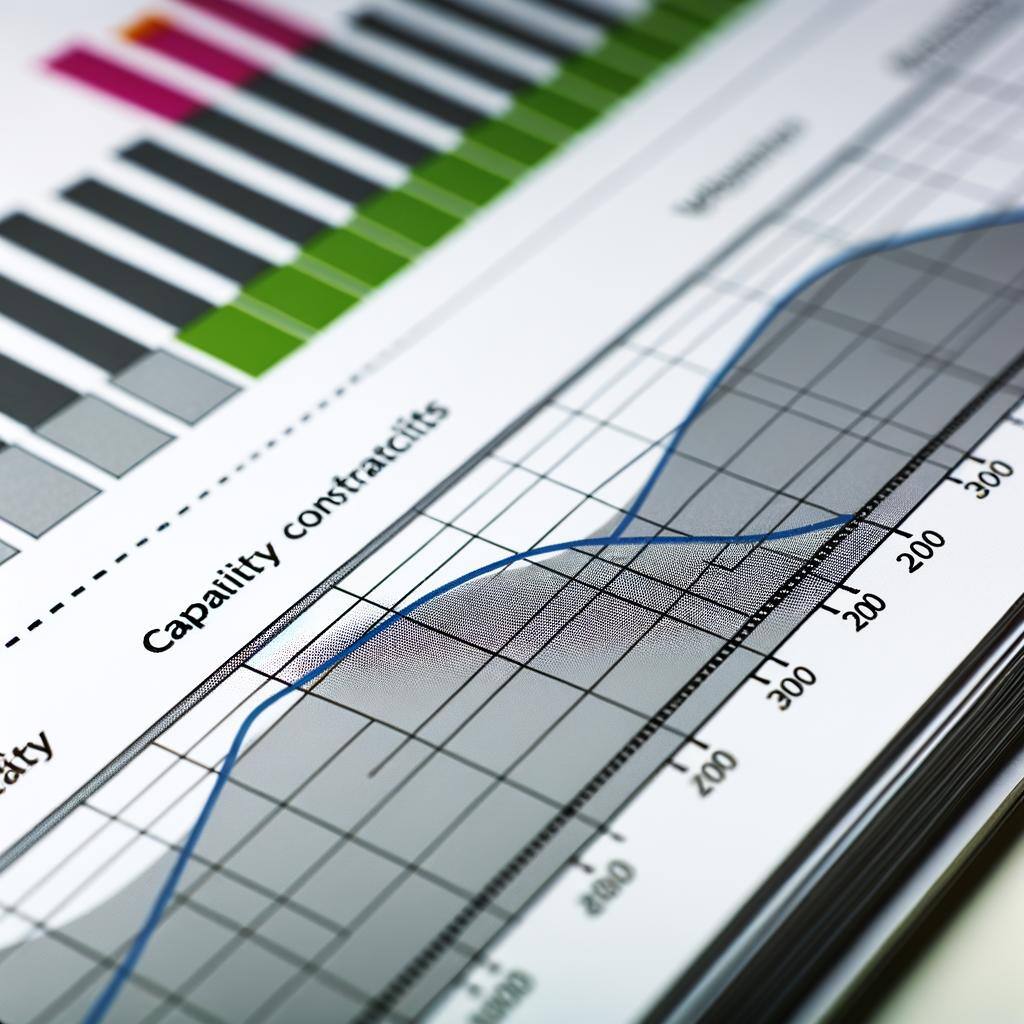
A surprising number of companies struggle with capacity challenges. It is surprising because people may assume that companies understand their demand and can adjust accordingly.
Capacity constraints arise when a manufacturing facility or system reaches its maximum output capability under existing resources, such as labor, equipment, or production lines. These constraints can manifest in several ways:
-
Production Delays and Backlogs:
Insufficient capacity can lead to delays in fulfilling orders, backlog accumulation, and missed delivery deadlines, ultimately affecting customer satisfaction.
-
Increased Costs:
Operating below full capacity often results in inefficiencies and higher production costs per unit, impacting profit margins and overall financial performance.
-
Risk of Opportunity Costs:
Inability to meet market demand due to capacity limitations can lead to lost sales opportunities and potential market share erosion.
Why Should Manufacturing Executives Care?
Manufacturing executives should prioritize addressing capacity constraints for several compelling reasons:
-
Operational Resilience:
Effective capacity management enhances operational resilience, enabling companies to respond promptly to market fluctuations and unforeseen disruptions. It is especially vital as there will always be unforeseen disruption. Few would have predicated that COVID would shut down the world or that a stuck container ship would block the most important waterway in the world. -
Customer Satisfaction and Retention
Meeting customer expectations through reliable delivery schedules and consistent product availability is crucial for maintaining customer satisfaction and loyalty. It is especially important in niche products with strong competition as failure to meet demand will push consumers to other products. -
Risk of Opportunity Costs
Optimizing capacity utilization reduces per-unit production costs, enhances profitability, and improves overall financial performance. Optimizing is the key word here as producing both too few or too many products can has per unit costs and lead to disappointing financial performance.
Situations Requiring Application of Strategic Principles
Manufacturing executives should consider applying strategic principles to manage capacity constraints in the following scenarios:
-
Market Expansion or New Product Launch
Introducing new products or entering new markets requires assessing and expanding production capacity to meet anticipated demand without compromising existing operations. Companies often struggle with new product introduction and are often beset by delays and quality challenges can reduce the potential impact and return on the new products. There is a lot that can be learned from Apple's approach and from understanding the bill of materials. -
Seasonal Demand Variations
Industries with seasonal fluctuations in demand, such as consumer goods or agriculture, need flexible capacity planning to adjust production levels accordingly. -
Supply Chain Disruptions
Unexpected disruptions, such as raw material shortages or geopolitical events affecting logistics, necessitate agile capacity management to maintain continuity in production. Companies, from our experience, understand the need to build resiliency but still do not really understand how to do it. -
Technological Upgrades
Implementation of new technologies or equipment upgrades requires aligning capacity expansion with technological advancements to maximize efficiency gains. There is often a "shining object" challenge with technology upgrades. Manufacturers upgrade their technology but not their processes so they do not achieve the capacity expansion that they hoped to. -
Economic Uncertainty
During economic downturns or periods of volatility, prudent capacity management helps mitigate financial risks and preserves long-term business sustainability. Economic uncertainty cuts both ways. Companies with poor capacity management can suffer if demand spikes or slumps.
Capacity is One of Critical Elements of Manufacturing
Capacity constraints affect everything from operational efficiency to customer satisfaction and financial performance. By understanding the profound impacts and strategic significance of capacity management, manufacturing executives can proactively address these constraints through effective planning, investment in technology, strategic partnerships, and continuous improvement initiatives.
In a competitive global marketplace, embracing strategic principles to manage and optimize capacity not only enhances resilience but also positions manufacturing companies for sustained growth and leadership. By prioritizing capacity management as a strategic imperative, executives can navigate complexities, mitigate risks, and seize opportunities for innovation and market expansion.