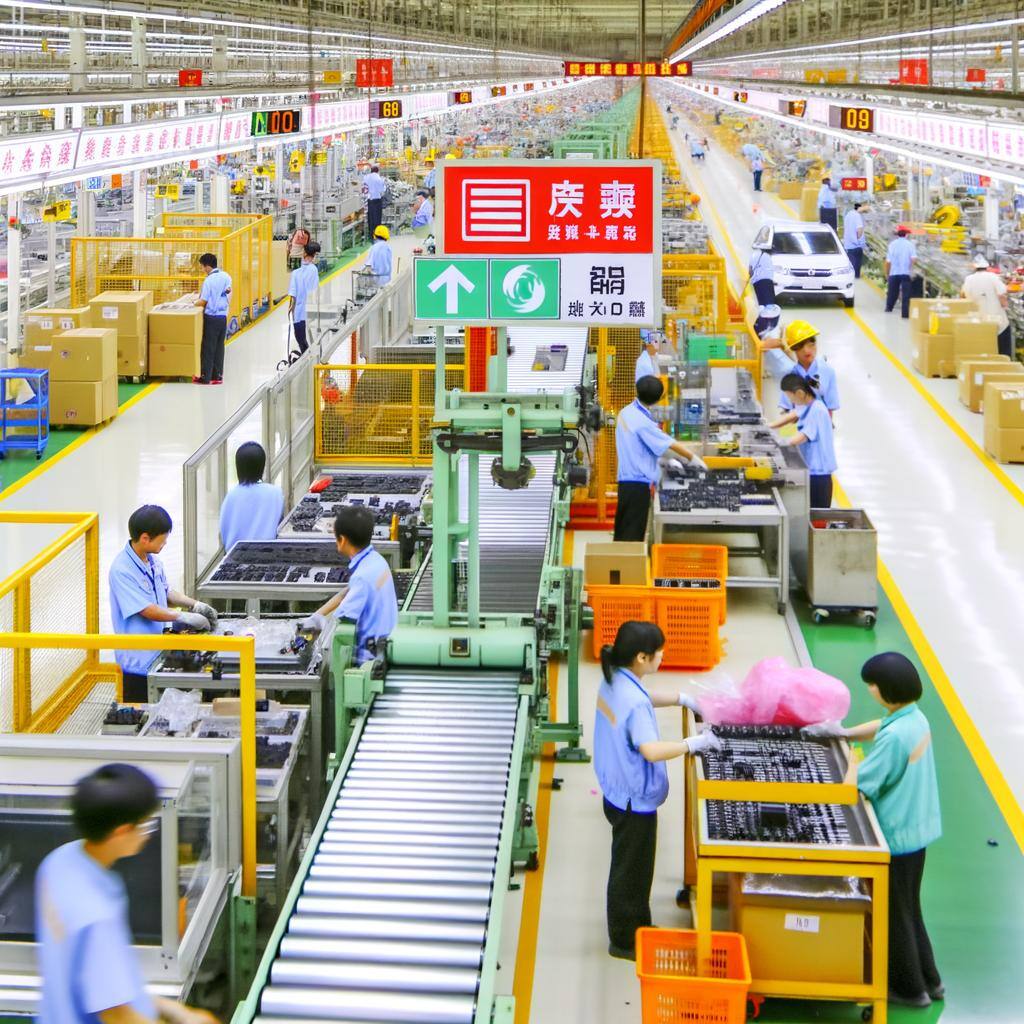
Chinese manufacturers have provided the world with both low cost finished goods, as well as low cost intermediate products. COVID’s impact definitely demonstrated the result of that unforeseen risk. Even after COVID, these key risks still exist independent of COVID’s impact.
Efficient inventory management is not merely a matter of operational tidiness—it's a strategic imperative that directly impacts profitability, competitiveness, and resilience. For executives overseeing operations that rely on Chinese manufacturing, the stakes continue to remain high.
This blog explores the risks of poor inventory management, and proposes leveraging principles from the Toyota Production System (TPS) as a proven methodology to mitigate risks and enhance efficiency.
How Does A Chinese Supply Chain Affect Inventory?
Since COVID, it seems like everyone is a subject matter expert on inventory management. With that said, though, ineffective inventory management can be costly, presenting excessive risk for manufacturing executives, especially when dealing with Chinese suppliers.
-
Excessive Inventory
Unless it is a long lead time item, stockpiling excess inventory ties up capital that could be allocated to more productive investments. It increases storage costs, risks of obsolescence, and ties up working capital unnecessarily. MTG has previously covered it in more detail here. According to a report by McKinsey & Company, excess inventory can tie up 20-30% of working capital in manufacturing companies.
-
Not Enough Inventory
On the other side, companies attempting to increase their cashflow may look at excess inventory to find cash. Insufficient inventory levels that cannot be easily remediated can lead to stock outages, disrupting production schedules and potentially causing delays in order fulfillment. A manufacturer’s most expensive asset is its production floor. This can damage customer relationships and lead to missed business opportunities. The Harvard Business Review has written a number of articles regarding inventory management and how to effectively levels based on your organization’s market position and other activities.
-
Inconsistent Quality and Lack of Visibility
It is critical to have regular tactical and strategic conversations with your Chinese suppliers. If quality is an issue and they are not committed to Continuous Improvement methodologies (like Toyota), resulting in inconsistent inventory levels and rushed orders. This increases the risk of receiving defective parts, leading to rework costs and potential production line stoppages. Quality Magazine discusses the impact of poor inventory management on quality assurance processes.
Applying Toyota Production System Principles
The Toyota Production System, renowned for its lean manufacturing principles, offers valuable methodologies to address inventory management challenges effectively:
-
Just-in-Time (JIT) Inventory
JIT principles advocate for maintaining minimal inventory levels by synchronizing production with customer demand. While this may seem obvious, our experience indicates that many organizations do not fundamentally understand how to do this, or how to accomplish this goal with the systems they have. More importantly, managing demand and production requires a level of internal structure to realize consistent results.
Using JIT minimizes waste, reduces storage costs, and improves responsiveness to market fluctuations. The Lean Enterprise Institute provides insights into JIT and its benefits in reducing inventory waste.
-
Kanban for Automatic Replenishment
Implementing a kanban system helps streamline inventory replenishment by signaling production needs based on actual consumption. As inventory is consumed, production systems signal procurement or operational teams that inventory needs replenishment. Kanban also promotes visual management and enhances communication between suppliers and manufacturers. Being your supplier’s best customer is not necessarily a bad thing.
-
Continuous Improvement (Kaizen)
Whether it is Toyota, Lean, Six Sigma, or Entrepreneurial Operating System (EOS), encouraging a continuous improvement culture fosters proactive problem-solving and waste reduction. By empowering employees to identify inefficiencies and implement solutions, companies can optimize inventory management practices over time. The Kaizen Institute outlines the principles of Kaizen and its application in improving operational efficiency.
Toyota Production System Works Everywhere
Poor inventory management can exact a heavy toll on manufacturing operations, which can be exacerbated by time zone, language and transactional issues. By embracing principles from the Toyota Production System—such as JIT inventory, kanban systems, and Kaizen—executives can mitigate risks associated with excess inventory, stock outs, and quality control issues. These methodologies not only improve operational efficiency but also enhance responsiveness to market demands and strengthen relationships with suppliers.
By integrating lean principles into their inventory management strategies, manufacturing executives can navigate the complexities of Chinese manufacturing while maximizing profitability and maintaining competitive advantage in a dynamic global market.
Still not certain about manufacturing in China? Discover more by clicking on the banner below.