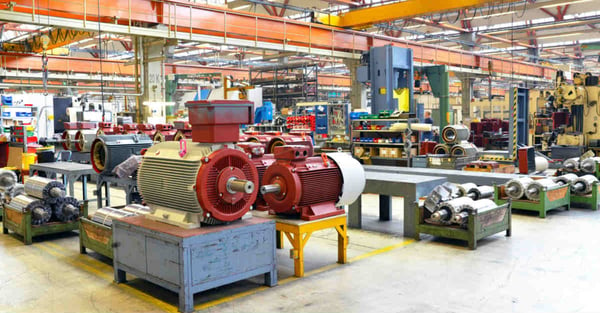
If your factory has invested substantial amounts in equipment, the controller probably wants to see if those machines & tools are used often for a productive purpose.
That’s the whole logic behind the indicator called overall equipment effectiveness (OEE).
The higher that indicator is, the more often the equipment is used for making good products.
Let's explore OEE in detail here...
1. What is the OEE?
The OEE is actually the product of 3 indicators:
- Availability (or ‘time use’)
- Performance
- Quality
Here is a great illustration of what goes into each of these 3 indicators :
The OEE can be calculated and tracked at the level of each piece of equipment, each workshop, and each plant. It is calculated as follows:
Availability ratio x performance ratio x quality ratio = OEE ratio
Let’s say a die casting machine has the following:
- Availability: 80%
- Performance: 90%
- Quality: 80%
These 3 indicators can be summarized into 1 ratio, the OEE, which is 80% x 90% x 80% = 58%. Not very high, but quite common.
Interested in this topic so far? You'll also enjoy our guide:
How A Preventive Maintenance System Cuts Costs In Chinese Factories
2. Is the OEE a meaningful indicator?
Its 3 components are interesting, taken separately.
However, can a local production supervisor, or even the production manager, be held accountable for all factors that are captured by the OEE? Certainly not. Here are a couple of examples:
- Purchasers and planners are responsible for shortages.
- Sales and HR agreements are responsible for working time.
That’s why we believe the OEE is too synthetic. In itself, it is not actionable.
3. Can the OEE be gamed?
Yes, definitely. Rewarding someone for a high OEE can lead to behaviors that are detrimental to the company’s performance.
Let’s compare 2 situations that end up showing the same OEE but very different performance in terms of cost, quality, and delivery.
- Bad approach: Running an SMT machine 24/7 and doing no preventive maintenance, with a quality of 70%, and making 1,000 pcs a day. No changeover means a lot of excess inventory. No preventive action means a high throw (i.e. scrap) rate, which is very expensive
- Better approach: Stopping the machine for regular cleaning and inspection and for small batch production, 95% quality, and 700 pcs a day. No excess inventory. Low throw (i.e. scrap) rate.
In companies where accountants alone decide on what KPIs are to be tracked, the ‘bad approach’ is quite common.
The book The Goal by Eli Goldratt makes this obvious. In the fictional example described, the production staff is requested to keep a large ‘monument’ piece of equipment running as much as possible, creating serious over-production.
Have you seen cases of over-production and insufficient maintenance & process control, with the aim of boosting the OEE? On the other hand, have you see cases where rewarding a high OEE led to virtuous behaviors? Leave a comment with your experiences or questions and we'll be glad to respond.