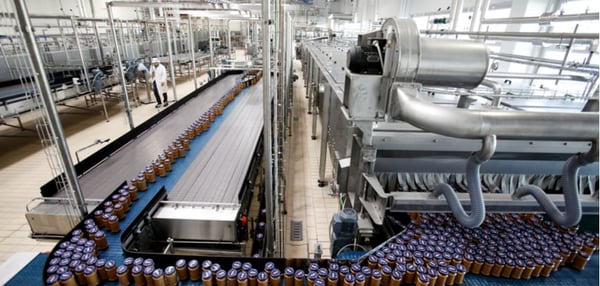
If you buy products from Chinese suppliers, you’ve most likely been horrified by some of the poor quality control systems you’ve seen.
In some cases, we managed to identify over 20 things that could easily go wrong within a mere 10-minutes walk on the shop floor—on fabrication & assembly or even on just a single product!
By our estimates, it would take a miracle for 99% of the pieces to be at standard. What causes such poor quality control practices? And what can you do to improve production efficiency?
Note: We know there are many excellent manufacturing facilities in China. However, we do need to acknowledge that the majority of factories in this country need a serious upgrade of their systems and processes. That’s what we’d like to address in this post.
What causes Quality Control failures in manufacturing?
Our sister company, SynControl, made this graphic on the most common quality control issues:
What are the typical issues shown here? To sum it up:
-
Poor quality delivered by suppliers
This is quite common, and a major source of issues. Once a faulty part is embedded in a final product, the whole product is already no good. A product can only be as good as the parts within it.
-
Inspection reports remain on paper
This is still the norm. Data collected might not be input into an integrated digital database (e.g. Excel sheet or specialized software), or it might be input days later. This can be problematic when trying to retrieve or store important pieces of information.
-
Poor data integrity
Inputting errors, fake data, and other actions that compromise the accuracy and consistency of data. All these mean that any conclusion made based on data can’t be fully trusted.
-
Only inspectors look at quality
Operators are rewarded on output quantity, not on quality (and that’s especially true if they are paid by the piece). They’ll do anything to reach their quota, even if it means cutting some corners. In managers’ minds, quality should only be looked at by inspectors.
-
Poor process for addressing problems
Not all detected issues are reworked, not all reworked pieces are re-tested, and immediate investigation & correction are rare.
-
No long-term view
Managers are too busy fighting fires every day. As a result, most don’t address problems at the root(s). Many issues end up bogging down the entire process for a long time.
-
Inconsistent results at end of line
All these issues could prove quite costly for any factory. I’ve previously written about the cost of internal failures and external failures on your bottom line.
How to improve Quality Control practices?
Setting up a quality assurance system is not easy. Here are the same operations, after an application like SynControl’s has been implemented in full.
Let’s look at it in detail:
-
Make key suppliers do self-inspections
You have some leverage over some of your main suppliers. Clarify your standards, train them if needed, and push them to do self inspections. It will be cheaper than getting some bad batches and having them do rework (in the end, you pay for that extra work!).
-
Make operators partially responsible for quality
Some of the inspection work should be done by the production operators themselves, and it can be done very well if you set the right incentives. It can often be done without slowing processes down or hiring anybody. You need fewer inspectors. You can cut on your QC budget this way.
-
Proper data collection, analysis, and alerts
All the QC data can be collected in 1 database and analyzed in real time. With this in place, workers can react while the issues are still “hot”, allowing management to find the point of cause much faster and make positive changes immediately.
Does this resonate with you? Leave us a comment below, or contact us, if you’d like to know more about this quality inspection app and how it can help you.
Does this resonate with you? Leave us a comment below, or contact us, if you’d like to know more about this quality inspection app and how it can help you.