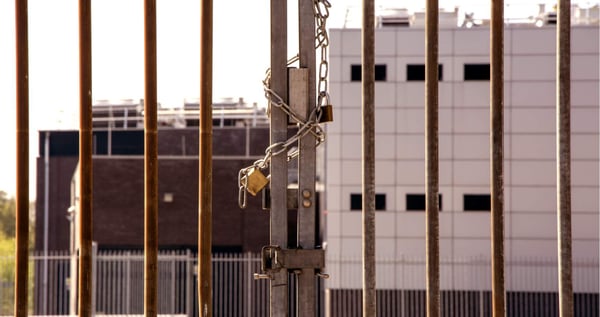
Will one of your key suppliers be unable to make production because of an anti-pollution inspection? Will they ask you to wait for 3-4 months? Will they just stop production until the factory gets to code? Factory closures in China like this have been happening over the past few months due to increased activity to combat pollution in china, so how can you know if you are at risk?
Factory Closures In China Due To Environmental Concerns Are Becoming Common
In the manufacturing sector, it seems everybody is talking about new and tougher environmental regulations in China. Actually, the regulations have (mostly) been in place for many years, and it was just that the government did not enforce them very well. Until now.
Will you find out your supplier does not even have a permit and have its operations shut down? (Again, a situation that has been happening much more frequently over the past year.)
Read more here about if social and environmental compliance is possible for Chinese manufacturers.
Let’s look a simplified case study to illustrate how to identify the major risks in your China supply chain, from an environmental standpoint.
A Chinese Supply Chain Case Study
A company buys a product made of 2 components – one in metal, one in plastic – from a Shenzhen manufacturer. That supplier only does assembly, inspection, and packing operations – all non-polluting in nature. They will probably not be threatened to shut down.
However, as you ask them to list the different processes necessary to make the components they assemble, another picture starts to appear…That Shenzhen factory might be unable to make production for lack of components.
Let’s look at the components one at a time.
1. Anodized and painted steel – factory closure is highly possible
The steel mill is certainly on the authorities’ radar. Coke is disposed to land fill, much smoke full of carbon particles pollutes the air (except if they have the equipment to capture these particles, but most do not), and many oils might end up in released water.
Switching from a steel mill to another is probably not very difficult, so that’s not risk No. 1.
One metal shop does the stamping and the cutting. And let’s say they also make the dies necessary for these processes. They need to use lubricants (petroleum products), solvents, and other liquids that might end up in rivers. That factory might be forced to close. And it might take 1-2 months to get another sub-supplier up and running in case new dies have to be prepared.
The anodizing is at high risk because of all the disposed water that might not be properly treated. This puts heavy metals into the ground water and rivers and anodizing factories have become a significant target of the government. In some areas it is impossible to get a permit for setting up anodizing operations now.
And the powder coating facility might also be closed any day because of air pollution issues… or simply because they don’t have the permit to operate a paint shop!
2. Thermoset plastic - factory closure is also possible
Making the plastic pallets is a petrochemical process that needs heating (high power consumption), washing (use of solvents and oil products that might end up in water), and drying (which releases volatile organic compounds from petroleum products). This operation is also certainly on the authorities’ radar.
Injection molding of thermoset plastic consumes a lot of power and might release some volatile organic compounds as well as some SO2 and SO4 (these gases are sources of high safety concern for operators, and can result in acid rains). This operation might also be shut down. And again, you might have invested in expensive molds that might not be made available should this operation be moved to another facility…
I hope this clearly illustrates the risks inherently present in most China supply chains.
The goods news is, there are solutions to address these issues. We will go over them in this follow-up article.