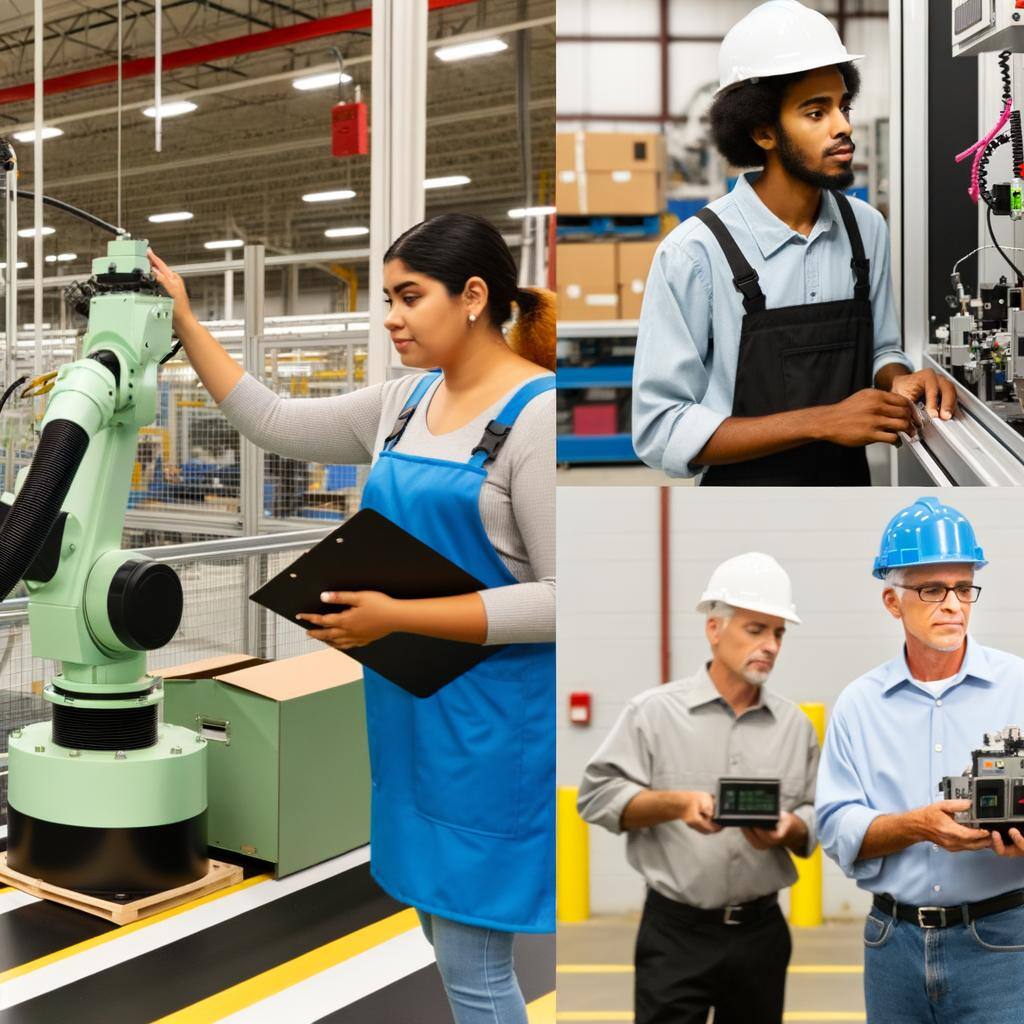
US manufacturing has faced significant challenges in recruiting and retaining skilled labor. For executives of small to mid-market manufacturers, these challenges can be particularly daunting. However, with strategic planning and proactive measures, there are ways to navigate through these obstacles and ensure sustainable growth and competitiveness in the industry.
The US manufacturing labor market is currently characterized by several key challenges:
Challenges in the US Labor Market:
Since COVID, it seems like everyone is a subject matter expert on inventory management. With that said, though, ineffective inventory management can be costly, presenting excessive risk for manufacturing executives, especially when dealing with Chinese suppliers.
-
Skill Gap
There's a noticeable gap between the skills required by modern manufacturing technologies and the skills possessed by the available workforce. LNS Research provided a statistic that showed that the average age of a factory worker has decreased significantly since 2020, which exacerbates the institutional workforce that retires every year. While trade schools continue to grow in popularity, it is not enough to keep up with the large labor demand.
-
Big vs. Small Companies
Larger corporations often have more resources to attract and retain skilled workers, leaving smaller and mid-sized companies at a disadvantage. The smaller companies will have to find ways to differentiate themselves versus the financial benefits that larger companies offer.
-
Changing Workforce Expectations
Millennials and Gen Z workers have different expectations regarding work environment, flexibility, and career advancement opportunities compared to previous generations. Manufacturing requires staff to be onsite. While the challenges that require addressing involve how to deploy technologies in this space, manufacturing is still viewed as a non-productive and dead end career choice.
Strategies for Overcoming Challenges
The Toyota Production System, renowned for its lean manufacturing principles, offers valuable methodologies to address inventory management challenges effectively:
-
Invest in Training and Development
Establish robust training programs to upskill existing employees and bridge the skills gap. Partner with local technical schools or community colleges to create pipelines of skilled workers tailored to your industry needs. According to the National Association of Manufacturers (NAM), investing in workforce training programs can yield significant returns in terms of productivity and employee retention.
-
Enhance Employer Branding
A study by Glassdoor found that companies with strong employer brands attract higher-quality candidates and experience lower turnover rates. Differentiate your company as an employer of choice by highlighting unique aspects of your workplace culture, growth opportunities, and employee benefits. Leverage social media and industry networks to amplify your employer brand.
-
Offer Competitive Compensation and Benefits
Conduct regular salary benchmark reviews. Consider non-monetary benefits such as flexible work arrangements, career development programs, and wellness initiatives to attract and retain top talent. The Society for Human Resource Management (SHRM) provides insights on competitive compensation strategies for small to mid-sized businesses.
-
Embrace Technology and Automation
There are so many new and interesting challenges related to manufacturing, many of them based in emerging technologies and how to support those both in and off the shop floor. Embracing these technologies can offset labor shortages and enhance operational efficiency. McKinsey & Company suggests that companies embracing automation can achieve substantial gains in productivity and competitiveness.
-
Collaborate with Educational Institutions and Community Organizations
Engage with local schools, vocational training centers, and community organizations to develop talent pipelines and promote careers in manufacturing. The Manufacturing Institute emphasizes the importance of industry-education partnerships in addressing workforce development challenges.
Labor is the Biggest Challenge Facing Manufacturers
Many of these suggestions are not new to manufacturers. While the labor market continues to challenge US manufacturing for small to mid-market companies are complex, they are not insurmountable. By adopting a proactive approach that includes investment in training, enhancement of employer branding, competitive compensation packages, adoption of technology, and collaboration with educational institutions, manufacturing executives can position their companies for sustained success and growth.
By addressing these challenges head-on and adapting to the evolving landscape of workforce dynamics, small to mid-market manufacturers can thrive in a competitive environment while attracting and retaining the skilled talent needed to drive innovation and productivity.
Still not certain about manufacturing in China? Discover more by clicking on the banner below.