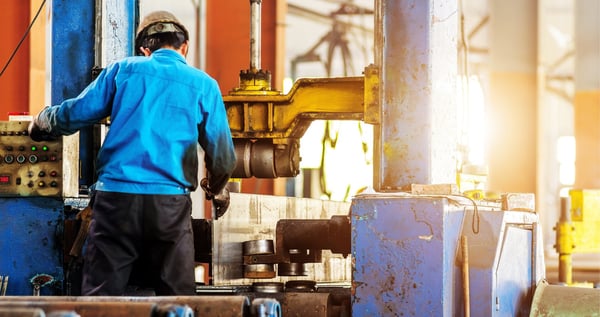
Does your production process include Computer Numerical Control (CNC) machining of metal parts? If it does, you might have recurring issues with your metal finishing as is common with this process.
One of the major challenges a CNC programmer faces every day is identifying critical metal machining parameters such as depth of cut, spindle speed, and feed rate. Traditionally, the starting point for this would be either a machining data handbook or the experience of senior machinists on the floor.
To get the best possible results from a CNC machine, you need to cover a lot of ground. First, you need to identify the goals you want to achieve, which can include:
- Optimizing material removal rates
- Maximizing tool life
- Quality surface finishing
The best practice for establishing the optimal rates for the material is to use a feeds & speeds calculator. By utilizing a materials database and knowing the detailed specification for each CNC machine, the ideal feeds and speeds rates can be calculated.
You will need to use different formulas for the different types of tools used within the CNC machine. Here we look at speeds and feeds rates for milling.
Calculating Cutting Speed
When using CNC machines, cutting speeds are important to understand as they can determine the efficiency your production can achieve. Having a cutting speed that is too high can incur extra costs as the cutting edge deteriorates quickly, but conversely, a low speed can reduce productivity and production rates.
Cutting speeds is calculated in Surface Feet Per Minute (SFPM) is a unit of velocity that describes how fast the cutting edge of the cutting tool travels, or in other words, it’s the speed at which the material moves past the cutting edge, i.e. the outside diameter, of the tool in feet per minute.
The simple calculation to work out the Rotations Per Minute (RPM) of the cutting tool is:
RPM = (4 x SFPM)/Cutter wheel diameter
Here are some standard SFPM you can use when working out the RPM for common metals:
- Mild Steel = 100
- Tool Steel = 70
- Cast Iron = 60
- Aluminum = 250
- Brass = 300+
For example, if you wanted to calculate the RPM of a 5/8” (0.625”) end mill cutting mild steel:
(4x100)/0.625 = 640 RPM
Calculating Feed Rates
Another important aspect to remember when implementing any CNC strategy is the feed rate. Generally, feed rate refers to the velocity at which the cutter engages the workpiece, and it is usually expressed in units of distance per revolution for turning and boring (typically inches per revolution [ipr] or mm per revolution).
Suggested cut feed rates can differ depending on the type of material you’re cutting, the cutter’s material, and a variety of other variables, such as the desired surface and the CNC machine’s characteristics. As an example, for milling, it is often expressed in units of distance per time (typically inches per minute [ipm] or millimeters per minute), while considering how many teeth (or flutes) the cutter has.
The calculation to work out the Feed Rate is:
FR = RPM x T x CL
Where each item is the following:
- FR = The calculated feed rate in inches per minute or mm per minute.
- RPM = The calculated speed for the cutter (as per the calculation above).
- T = Number of teeth on the cutter.
- CL = The chip load. Chip load, also referred to as feed per tooth, is a term used to describe the thickness of material removed by one tooth on the tool's cutting edge. The chip load is the radial depth of cut the cutting tool makes in one revolution. The chip load value is normally provided by the tool supplier, such as the sample below:
For example, to calculate the feed rate for a 5/8” end mill cutter with 4 flutes from the table above, you'd use the following formula:
FR = 640 x 4 x 0.004
FR = 10.24 inches per minute (ipm)
Choosing Your Cutting Fluid (Coolant)
There is a wide variety of cutting fluids available today. Many new coolants have been developed to meet the needs of new materials, new cutting tools, and new tool coatings.
When machining, the heat generated by friction at the tool-workpiece interface has a significant impact on many machining processes. The rise in temperature at the contact zone significantly increases tool wear and, as a result, tool life.
The primary functions of cutting fluids are to:
- Cool the tool, workpiece, and chip;
- Reduce friction;
- Prevent or reduce chip welding and built-up edge formation;
- Prevent rust and corrosion;
- Flush chips away.
The goal of metal machining operations must be to improve productivity and reduce costs. This is accomplished by machining at the optimal speed while maintaining practical tool life, reducing scrap, and producing parts with the desired surface quality. By ensuring proper selection and use of cutting fluids you can achieve all of these goals.
Setting Benchmarks
There are a variety of vital factors that influence the optimal speeds and feed for your project. These include the tool, material, fixturing, chip removal, and tool path type.
There is no such thing as a one-size-fits-all list of speeds and feeds. Every project is unique and may require some experimentation to find the setting that works best. The goal, in the end, is to produce a part that meets your requirements. It will be easier to fine-tune the settings once you understand how each input affects the final result.
While trained machinists can often measure and optimize each setting, most people can get away with a bit of trial and error. Rather than stressing over every detail, begin with your best guess and go from there. You may break a few tools along the way, but you’ll quickly develop an intuition for speeds and feeds, and know which areas need improvements.
Using Speeds and Feeds Formulas
Before you leverage metal machining to its optimal capacity, you need to clearly define your manufacturing goals. These goals will determine the best rates for your production processes which your CNC programmers can then set.
In some cases, it may be more profitable to run faster for higher production and replace the tools more often. And in others, it may be better to run the tools more slowly for endurance and allow the machine to operate unattended. By considering all the above aspects when it comes to CNC machining of metal parts, you may make different decisions based on the value you associate with the results.
Have you experienced issues with metal finishing?
Download our complimentary white paper to learn more, or leave a comment below!