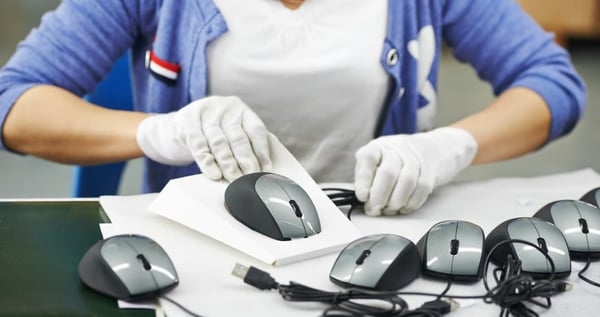
The vast majority of products need some type of assembly before they are shipped to customers. Hence, enhancing assembly operations is something most manufacturers should aim at.
Unfortunately, best practices in this area are well known among industrial engineers, but are not applied widely across factories, especially in countries like China or Vietnam.
In this article we’ll look at a logical approach to improve assembly, inspection, testing, and packing operations.
1. Getting the parts to move
In 1913, the Ford Motor Company got some inspiration from a slaughterhouse that was moving carcasses on a conveyor. It was actually a “disassembly” line, but the concept could be transferred to assembly!
Ford moved from “bench assembly” (all the parts come to the car, which gets assembled without moving by a few specialist craftsmen) to “line assembly” (the parts and sub-assemblies move through the hands of many workers who are stationed on their process).
The result? Productivity was multiplied by 4. However, we still see some bench assembly in Chinese factories, especially in cases where the workers and group leaders were tasked with organizing their work by themselves.
Moving from bench to line assembly is a change we often implement in the course of our work, as detailed in the following lean manufacturing case study which you can download for free:
>>>Hunter Auto Factory Turnaround Case Study<<<
The concept of the assembly line has been applied to virtually all types of products. Even some large Boeing planes are loaded on a ‘crawler’ conveyor and move slowly ahead.
Image credit: Allpar.com
2. Getting assembly workers to focus on their work
The goal here is to increase the proportion of the time spent on value-adding tasks. For example, transforming the materials is value adding, while moving them is not.
In most Chinese factories we have assessed, the ratio of value-added time is around 10-15%. It means they spend at little as 6 seconds in a minute on tasks that are actually value adding. This often comes as a shock to their managers!
One simple change that can be done quickly is a new organization of internal logistics:
- Having internal logistics operators replenish materials, move boxes, etc. (A few changes in the layout might be necessary – for example displaying materials in smaller boxes and in gravity-fed racks.)
- Having production operators simply pick the materials, process them, and put them down (in an easy and safe manner)
If operations are connected and can be done one after the other without waiting, a conveyor belt is often a convenient way of minimizing the handling of pieces. A rolling table is cheaper and more flexible, but a conveyor belt also ‘paces’ the work. There are pluses and minuses to each solution.
3. Getting the parts to “flow” as much as possible
Connecting sub-assemblies to the main assembly line as tightly as possible is always a positive change. However it is not always possible – It might necessary to make sub-assemblies in a separate workshop or building… or it might be possible to place them just along side the “main” line as shown in the simplistic example below:
Another obvious change we have implemented in many factories is the integration of assembly, testing, inspection, and packaging:
For some reason, packaging is disconnected from assembly most of the time, but it only adds to the waste in the entire operation (piling up pieces, waiting, preparing and piling up packaging materials, move them close to the point of packaging, lots of unnecessary handling, etc.) Integrating the steps closely, as shown above, is a big boost for productivity.
4. Enhancing assembly operations through better balancing
Some of the assembly work might use specialized equipment (e.g. molding the plastic connectors at the end of cables) while others can be done quickly with simple tools. It means some operations are inherently faster than others. That’s a recipe for an imbalanced line.
A junior engineer can break the process down to discrete steps and count each step’s time for a few cycles (including the time spent picking the components, moving them, etc.). It typically looks like this:
As you can see, this process is not balanced. Step 2 takes 25 seconds! If you can make it faster, the next bottleneck is step 5 (23 seconds), then step 9 (22 seconds), etc. In the meantime, steps 4, 8, and 12 get done much faster (operators are under-loaded).
Ideally, you can get no step to take longer than 20 seconds. And you can combine 2 successive fast steps (in this case, 3 & 4 and 7 & 8) in 1 step. A much better balanced line would look like this:
Note that step 12 is still much shorter. But it can be handled by the line leader, who uses her free time to watch & adjust a few variables.
It looks easy, but it might be a lot of re-engineering work. How to get a process step from 25 seconds down to 20 seconds?
One solution is to increase the resources – for example one more operator, or one more machine.
However, management should look at solutions for improving the productivity of those operations – thus reaching the desired result without increasing spending/investment. It usually involves a combination of these solutions:
- Looking for a better method, and documenting it in work instructions
- Better tooling/jigs
- Mistake-proofing the operation so the operators don’t need to double-check certain aspects of their work
- Semi-automation, for example automated unloading, enabling one-hand operation, etc.
What do the best assembly lines look like?
I would say, it depends on your philosophy. Here are three examples:
- Full automation, or close to full automation: this is the dream of many Chinese factory owners who are tired of managing a workforce. The downside is a lack of flexibility and a much increased need for maintenance and setup skills.
- A U-shaped cell manned by several operators: this is often the desired end state in a lean transformation. It takes some cross-training to work really well.
- A cell manned by only 1 operator: this is often desirable for the operator’s sense of purpose, since he can see the product getting built from A to Z. It is also good for productivity. But it takes extra training efforts!
What have been your experiences? Have you see very well setup assembly lines, and what were they looking for? Share your questions, commentsor experiences below and start the discussion!