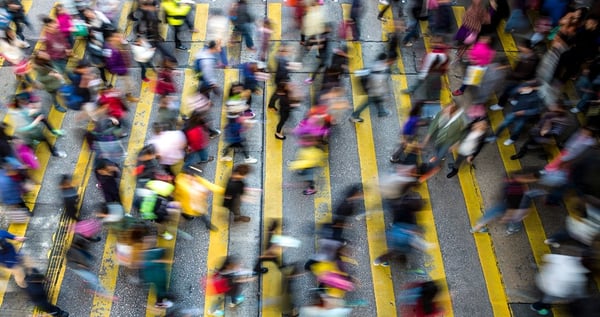
In 1980, NBC produced a great documentary entitled “If Japan Can ... Why Can’t We?”. It changed many American businesspeople's mindsets, and is credited for starting the "quality revolution" movement of the 1980s.
At the time, American manufacturing was suffering more and more after decades of great results. Any similarities with Chinese manufacturing these days? You bet.
Here are some of the issues American manufacturing was experiencing in 1980:
- Declining productivity gains
- Stagnating demand
- Adversarial management/labor relationships
- Lack of respect for employees
- Short-term focus of managers and executives
- Tendency of company executives to find ways to avoid regulations rather than comply
- Low interest of company executives to learn new ways of doing business (in 1979, 20 times more Japanese businesspeople came to visit US companies than the opposite)
- Lower quality and productivity than some competing nations
Looking back at this video and at the reaction of many American companies can make China optimistic. A growing number (but still a minority) of factories have changed their culture and their entire approach to managing their business. Managers and supervisors had to change their mindsets and their attitudes.
Deming's approach was presented as the reason why Japan became so successful, and the key to emulating their success. In his words:
[The Japanese] realized that the gains that you get by statistical methods are gains that you get without new machinery, without new people.
The journalists place a very heavy emphasis on statistical tools, but we hear Deming mention other important concepts (inspection and rework are waste, building in quality is key, most issues come from the system and depend on management, etc.)
This program is quite significant from a historical perspective. The US and Europe were starting to understand that their economic problems were due to the supply side (decreasing productivity gains) and they should stop applying demand-side measures dictated by Keynesian economics.
One downside of this documentary, however, is the high number of shots of automated equipment. The narrator insists several times on the importance of employee engagement, but most viewers probably remembered the complicated machinery better.
This might be one of the factors that pushed a few companies, such as General Motors, to invest heavily in production facilities that can be run without humans. We touch on this in our infographic about manufacturing practices.
Finally, the documentary didn't really do a good job of explaining why quality improvement and productivity gains (due to process improvements, process control, and other approaches) go hand in hand and can be pursued simultaneously.