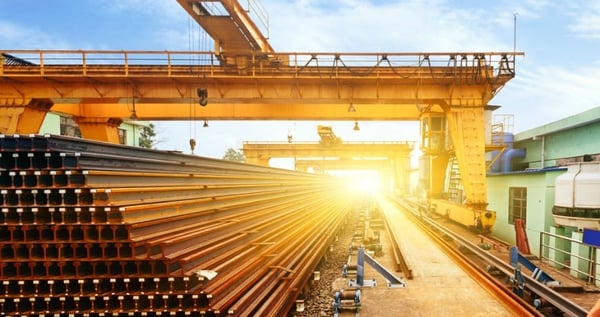
In a previous article we touched on how excessive inventory costs factories money but I would like to expand on a little in this article.
Wherever there are instances of inventory building up throughout the manufacturing process there will inevitably be elements of waste, two of these elements are highlighted here, motion and waiting waste:
Motion Waste:
A poor factory layout where there is a distance between work stations means the parts have to be moved between one work station and then next. The more a product has to travel throughout the entire manufacturing process, the more motion waste there is, this translates into unnecessary cost which in turn affects the price of the product.
Motion waste can also be seen at individual work stations were workers have excessive movements to bend, stretch, and lift items from the floor or actual walk to get the products they need to process.
Waiting Waste:
This occurs when products are physically not moving through the production process. If there is wait time for a product to get processed of twenty minutes, that twenty minutes that can never be recovered and has to be paid for in the overheads of running the factory, again, this directly affects the price of the product.
In both of these cases there would most likely be excessive inventory from either bottleneck processes or from batch queue type manufacturing, either way; the impact is unnecessary cost to the factory which could be reduced.
Cost Impacts on a Chinese factory
There are often times when a Chinese factory would borrow funds from a bank in order to maintain operations, most of the time it’s to purchase raw material for processing into products. This will have an impact on the price of your product. Ironically, a lot of the time this could be avoided if inventory were to be reduced.
Cost of Borrowing:
For a factory to borrow from a bank in China it is relatively easy but the actual cost is from 5% to 8%, this has to be factored into the overhead calculation of the factory.
Before setting a price for your product, the factory would have to know the costs of running the business. To determine how much it costs to run that business, the following needs to be included: cost of property and/or equipment leases, loan repayments, inventory, utilities, financing costs, and salaries/wages/commissions, plus other attributes like waste as discussed above.
Cost of the Warehouse:
The impact on the price of your product is influenced by around 1% just through the cost of running the warehouse including its entire staff. If excessive inventory could be reduced in the warehouse then this would have a positive effect on the cost of manufacture.
Cost of Obsolescence:
Another major issue with larger batch sizes where WIP inventory builds up is a product change request implementation that renders that inventory obsolete and consequently being scrapped off. The cost of obsolescence can sometimes be as high as 15% especially when products are highly customized, therefore, by keeping the WIP inventory as low as possible would reduce the impact of any change implementation.
Cost of Not Selling:
The main objectives of every factory are to produce goods and sell them. This may sound blatantly obvious but we see all too often masses of invent either piled up as WIP throughout factories or as finished goods waiting to be sold. Either way, product not being sold costs factories on average 10% of their turnover, all because they have excessive inventory in one form or another.
The conclusion to this quick insight into the cost of inventory for your Chinese manufacturer clearly shows that inventory needs to be reduced and managed from a workflow point of view. The reduction in inventory will reduce the overall cost of production of your goods and potentially eliminate the need for a factory to borrow from a bank.
What do you think?