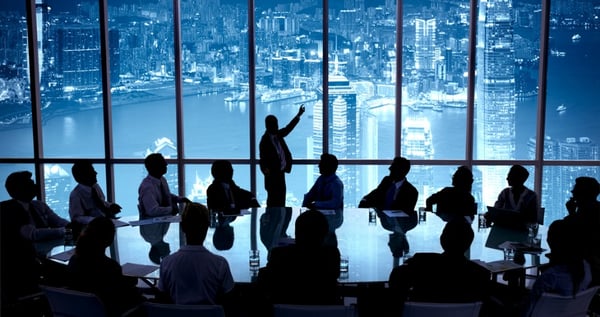
Jeffrey Liker and Gary L. Convis, a former executive V.P. of Toyota, mention two great analogies in their recent book:
Continuous Improvement is Like a Diet
Implication
If you relax after 6 months, most of the benefits will disappear.
Cause
Some of the steps we push factories to take are counter-intuitive. If a new general manager arrives after one of our missions, he can get back to a typical "batch-and-queue" organization in just a few weeks.
Example
Reducing the batch size and avoiding over-production are among the best ways to reduce total production costs per unit. But it is human nature to assume that larger batches are always more efficient.
A Continuous Improvement Program is Like an Investment in Education
Implication
Some of the changes we implement in a factory can't be tied to a specific ROI.
Cause
We try to avoid "point improvements" here and there (except if that's what the client specifically asks for). Rather, we need to have a coherent plan that impacts the whole production cycle, rather than a specific process. That's how large benefits are ensured.
However, this coherent plan is made up of many elements whose ROI can't be calculated individually.
Similarly, if a students calculates the ROI of a certain course, he cannot see a direct cause-and-effect relationship with the benefits he will get out of it in the long term.
Example
Reducing the setup time of a pressing machine helps save a few hours here and there. But, more importantly, it makes it easier to make smaller batches, and it pulls operators away from the mass production mentality.