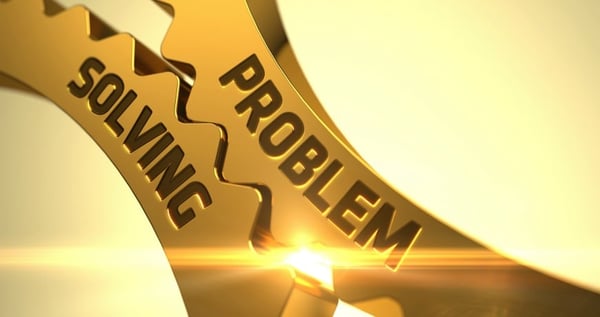
Have you even wondered why brands such as Toyota, Lexus, or Honda tend to score the highest in customer satisfaction? Why is their quality consistently top notch?
The short answer is, they have excellent systems in place to detect, analyze, and solve quality issues. In this article I will focus on two lean problem solving tools they use every day...
1. Detect Quality Issues as They Happen
I have visited hundreds of Chinese factories over the years. The typical situation when a quality issue pops up is as follows:
- The operator closest to the process that generates the issue doesn’t do anything special – he just passes the products along to the next process.
- A line leader might notice the issue by chance, or an in-process inspector might notice it.
- Nothing happens for a while. It is put aside and waits for a manager’s decision.
- If they deem it as a serious issue, they will look around to understand how it happened.
- They will make a change and then forget about it until they somehow detect the same problem again.
- They might, or might not, re-work the goods.
Instead, what should happen? In the best factories, here is the typical work flow.
- Production operators are responsible for what they make. They segregate the bad pieces they notice.
- The team leader or supervisor will see the bad pieces – they are typically shown prominently, for example in small red bins that get full quickly.
- Since several bad pieces with the same type of problem came up in a short amount of time, an investigation is launched.
How do they investigate the issue? They follow a certain method that has proven its value.
2. Following a Structured Problem Solving Approach
Again, this is quite different from what the average factory manager does in China. They tend to take shortcuts:
- “Can I think of a reason for this issue?”
- “Yes it is probably due to XYZ. Let’s change it.”
- “Done. Let’s get to the next problem.”
(We dived into an example of this approach in a past article about problem solving challenges.)
So, what processes do the best companies follow? This approach is at the core of lean problem solving tools.
- Clarify the problem – collect data until you have a good grasp on what is wrong.
- Break down the problem -- analyze your findings. Is it due to several problems?
- Set a target – what level of improvement should we aim at?
- Analyze the root cause(s) – observe the situation and try to understand deeply the HOW and the WHY, down to the root cause(s).
- Think of corrective action(s) – what to do to avoid recurrence of this problem?
- Implement corrective action(s)
- Monitor results and process – was the target achieved? If not, why not? Should we start over again?
- Standardize and congratulate.
Together, these 2 tools comprise what Nissan, Valeo, and other companies call QRQC (Quick Response Quality Control), and what Toyota calls Practical Problem Solving. It sounds like common sense but I would guess it is really applied in less than 2% of factories worldwide…
>> Click here to tweet this blog post to your network <<
Your Thoughts On These Lean Problem Solving Tools?
What kinds of systems, if any, are you using to assure quality in your factory, or are you seeing in your supplier's factory?
Are there plans in place to make a change, if so, what are you looking to implement?
Feel free to ask any questions you may have or share your experiences with our community by leaving a comment below.