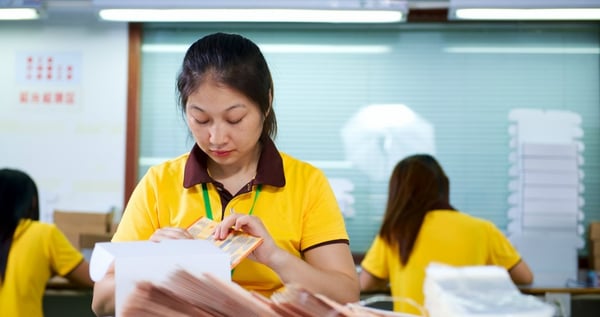
Chinese organizations, with the notable exception of businesses founded by ex-military personnel, tend to be very ‘light’ when it comes to using management tools. Their customers notice the lack of systems and wonder, where to start?
In this article, we present two simple lean management tools that can be introduced in any factory and align the organization behind common goals without increasing costs...
Lean Management Tool No. 1: Key Performance Indicators
Does everybody know precisely on what basis their performance will be evaluated? And can all employees say what being “good” at their job consists of? If not, one of the first things you need to do is give them a few KPIs.
Ideally, a set of KPIs should be cascaded throughout the organization. Here is a simplistic example:
- The general manager is accountable for cost, quality, on-time deliveries, safety, morale
- The production manager is accountable for efficiencies, on-time delivery, safety
- A workshop supervisor is accountable for efficiencies, on-time delivery, safety, and 5S in his/her area
- A team leader is accountable for quality, respect of target number of pieces, and safety in his/her area
- A production operator is accountable for respect of target number of good pieces of his/her team
To start with, it does not have to be more complicated than that.
Each employee should know how they will be evaluated, and whether they are doing better than before. Ideally, no one has more than 5 direct KPIs. (Research has shown that someone can keep in mind and work on 1, 2, or 3 priorities. A longer list makes it less likely that the highest priorities will get the attention they deserve.)
Side note: Some people may not agree with what we wrote here. Here are two common objections:
- “KPIs are not Lean.”
- “You are describing management by objectives, which is different from Lean.”
Let us respond to these objections.
Lean management puts a lot of emphasis on “management by means” rather than “management by objectives” but people still set targets and pay a lot of attention to data. The difference is what metrics are used for. The question is not “will you reach your target, yes or no?” but rather “what process to follow in order to reach your target?” and then, later, “have you followed the process we outlined, what was the result, and what can we learn from that?” This is management by means.
Lean Management Tool No. 2: Visual Management
Is data communicated throughout the company? Probably not.
In most Chinese factories, the only numbers production operators and leaders see is the number of pieces they have made, since it determines their pay. And office workers are not sure what other departments are working on.
We already wrote about it in The 5 Issues Your China Factory Turnaround Strategy Should Address, but the solution is really simple. The KPIs of teams, workshops, and departments should be posted in a way that is visible to all.
Targets should be in place. Ideally, KPIs should be color coded (e.g. green, orange, and red) and managers should be able drill down in to the details easily when necessary.
Another key element is that employees should be able to link their achievements to the company’s overall performance. They have to understand that scrapping material that could be used hurts margins, and at the same using material that causes quality issues down the road also hurts margins (with much higher impact). Without that knowledge, employees cannot be counted to make informed decisions.
Conclusion
Once a manufacturer has implemented these lean management tools, pushing new initiatives throughout the organization becomes easier. Make it a KPI for certain people, give them a target, communicate about it, and provide support and resources where needed. Effectively it allows a company’s management to push improvements faster and with a higher success rate.
Which lean management tools have you found to be useful in your factory (if any)?
Do you have any questions about KPIs and visual management?
Please add them as a comment below this post.